1.板金部品
入社間もない頃は、いきなりクランクの設計を任されることはまずない。結果、板金部品の設計が多いはず。けれど案外その実態を知っている人は少ないと思う。
SPHとSPCの違いくらいは最初に教わると思うが、おさらいをしておくと、SPHは熱間圧延鋼の名のとおり、鉄が熱いうちにロールにかけられた鉄板で、主に厚板として使用し、厚みのバラツキもやや大きいが、コストは安い。SPCはSPHを更に冷間圧延して薄く延ばしたもので、薄板はこちら。精度も高いが手間がかかっている分コストも高い。
板金部品は、基本的にプレス加工で成形するが、まず、知ってほしいのは、加工後の製品には表裏があるということ。
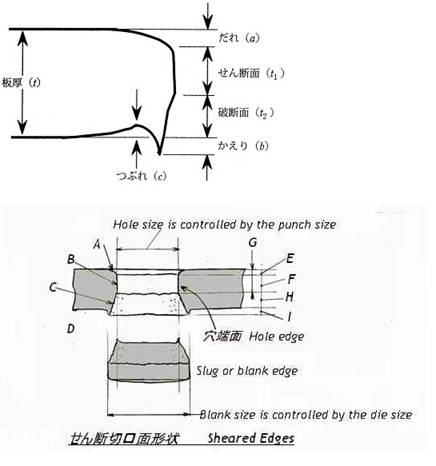
上の図は、プレスで打ち抜いた鉄板の断面だ。プレス金型は、上側をパンチ、下側をダイと言うが、パンチとダイの間には小さな隙間がある(板厚によって変える)。打ち抜くときに塑性変形する部分(せん断面)と破断する部分とがあって、塑性変形した側(この図で上面側=パンチ側)にはダレが生じ、破断した側(ちぎれた方)にはカエリが生じる。
これがエンジン部品で問題になるのは、例えばオルタネータのアジャステイングバーのような重要部品だ。取り付け相手部品とは全面で当たるが、ボルト側はワッシャ径でしか当たらない。当然、ボルト側の座面面圧は高くなるので、その面圧を低くするために、ダレのない側がボルト側になるようにしないといけない。そうするには、プレスの打ち抜き方向を図面で指示する。板厚が厚い程ダレは大きく、極端な場合ワッシャが線当たりになってしまうと、そこがヘタってボルトの軸力低下をもたらす。
すべての部品に打ち抜き方向指示をする必要はないが、指示をしたからといってコストが上がることは少なく、設計者で必要かどうかをよく考えて、必要なら忘れないように指示をすること。特に板厚が厚く板幅の狭い部品は、ダレが大きくなり、平面部がほとんどなくなるようなケースもある。ボルトのワッシャについても同様で、必要に応じて表裏を指示する。ただワッシャの場合は、内周と外周では打ち抜き方向が逆になるので(穴を開けてから外周を打ち抜くため)、よく考えて指示してください。
このダレやカエリがあってはならない部品の場合、ファインブランキングという工法がある。抜く側も抜かれる側も、金型で挟み込んで、ほぼ100%せん断面になるように打ち抜く。型費がかかるのでコスト高にはなるが、プレスしたものを後で加工する場合に比べると、生産数が多ければコストダウンになる。
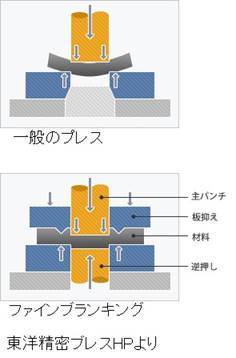
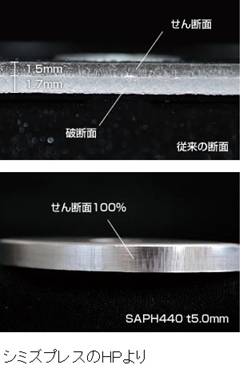
長々と説明したが、これが板金部品に表裏があるということで、もし知らなかったとしたら、これからの設計に役立ててください。
ちなみに、せん断面の板厚に対する割合をせん断率と言うが、これが重要なのは、例えばサイレントチェーンのように、穴に面圧がかかるような場合だ。
量産車の場合、イニシャルコストよりもランニングコストを抑えた方が原価低減になるので、板金部品は板厚を抑えるために出来るだけ薄くするのが常識だ。軽量かつ高剛性にするために フランジ、エンボス、曲面化などの手法を用いると思うが、その際の注意点をいくつか挙げておこう。
板を曲げた時、曲げの中心がやや外寄りになるのは、誰でも想像が付くが、フランジの先端がエッジになるのは気付かないこともあるのでは(特に短いフランジで)。曲げの外側は引っ張られ、内側は押されるので、フランジの先端では内側が外側より高くなる。つまりエッジになる。組立作業者がケガをすることもあるだろうし、ユーザーが手を切るようことがあると、大きなコンプレインになるので、人の手が触れそうな部位は注意が必要だ。量産設備で作られた試作品をよくチェックして(試作品は手直しが入るので、見逃す可能性がある)、問題がある場合は、バレル研磨やショット、塗装などで対策する。
近年、プレス加工技術が格段に進歩して、最小Rの制限はなくなったに等しいが、そうは言っても、ゼロRなどを指定すると、それなりに工程がかかり、コスト高になる。どれくらいが適切かは板厚にもよるので一概に言えないが、Rが小さすぎると応力集中も大きくなるので、生産技術部門や仕入先の言い分も聞いて、合理的な設計を心がけるようにしよう。
エンジン部品では共振は回避しないといけないので、ブラケット類の剛性は高く設計すると思うが、同一変位、同一入力の場合は、剛性が高い分応力集中もしやすくなるので、剛性を高めつつ応力集中しない設計が重要だ。「疲労破壊のメカニズム」にも書いたが、図面が書きやすいからと言って同一Rで設計するのでなく、フランジの曲げRもコーナー部だけは大きくするなど、応力集中を避ける工夫をしよう。
近年のプレス加工技術の進歩は目覚ましく、これまで鍛造や焼結で作っていたものも、どんどんプレス鍛造に置き換わって来ている。複数の部品の一体化まで出来るようになって来ているので、コストダウンの手段のひとつとして考えてみてもよいのでは。
2.アルミダイカスト
若い設計者が、板金部品と同様に接する機会が多いのが、アルミダイカストではないかと思う。
アルミダイカストの製造工程のイメージは、下記のリンクを参照してください。わかりやすい動画で見ることが出来ます。
http://www.kobac-j.co.jp/die_casting/process.html
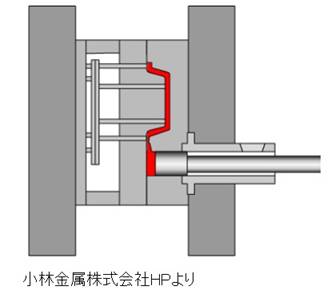
アルミダイカストは、溶けたアルミをプランジャーで型内に高圧射出するため、アルミの溶湯が型内の空気を巻き込んでしまう。なので、表面はきれいでも、中はザクザクだというイメージを持った方が正しい。そのため、アルミダイカストは一般的に熱処理が出来ない。中の空気が膨らんで、ワークを不良品にしてしまうからだ(ブリスターと呼ぶ)。それを防ぐ工法として、あらかじめ型内の空気を抜く真空ダイカストと呼ばれる工法がある。
もう一点、代表的な欠陥は、ヒケ巣だ。これは、溶けたアルミがまず表面から固まり、その後内部が固まる時に、体積は小さくなるが外側が固まってしまっているために縮むことが出来ず、中が空洞になる、または裂けてしまう状態を言う。なので、空洞部分は基本的には真空だ。粗材を加工した時に、このヒケ巣が内外に貫通して、リークテスト不合格、すなわち不良品となる。大物部品では、多かれ少なかれヒケ巣や気泡は発生するので、その状態によっては使用しても差し支えない場合もあるが、ないに越したことはない。
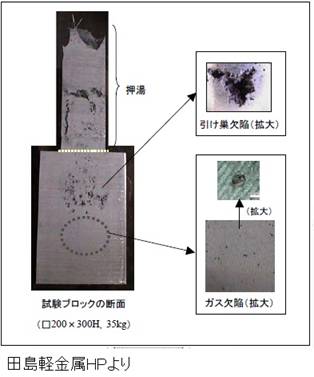
これを防ぐ最もシンプルな方法は、厚肉部を作らない設計だ。これが大物部品(代表的なものはシリンダブロック)だとなかなか難しい。肉をぬすむために型を追い込んでいくと、焼き付いたり破損したりする。そもそも型は基本2面で、スライド機構を使っても6面まで。ダイカスト中子などというスゴ技も世の中にはあるにはあるが、相当特殊な技術を要する。ダイカスト型には冷却のための配管が張り巡らされていて、それとの取り合いもある。それでも設計者は悩み悩みながら、とにかく厚肉部を減らす方法を考えないといけない。そのためには、とにかくあちこち断面を切りまくって、まず厚肉部(駄肉)を探し出すことだ。駄肉を見つけたら、抜き方向をいろいろ変えて、少しでも多く駄肉をぬすめる形状を考える。いろんな制約の中で答を見つけるのが難しいからといって、生産技術部門からの要望を待っているようでは、一人前とは言えない。
リークテストに不合格になったものを、含浸(有機含浸、無機含浸)という工法で救済する方法もあるが、それは最後の最後の手段。
小物部品で絶対にヒケ巣があってはならない、例えばフューエルデリバリパイプなどは、スクイズダイカストといって、アルミが固まる寸前に、注湯部とは別の小さなプランジャーを押し込み、空隙をなくす工法がある。真空ダイカストなどと合わせて、無孔ダイカストと呼ばれている。
アルミダイカスト部品で、よく問題になるのが、押し出しピン座とバリ残りだ。
アルミは鉄製の型より熱膨張係数が大きいので、固まる=冷却すると型に食いついてしまう。そのため、抜き勾配を付けてはいるが、ピンで押し出してやらないと型から外れてこない。そのピンを受ける座が押し出しピン座で、生産技術部門の検討項目になるので、初期の設計時には図面(モデル)反映ができない。良質な生産には必ず必要なものではあるが、ギリギリの隙関係で設計している設計者には、好き勝手に付けられると困る部位もあるはずだ。なので、そういう部位には、あらかじめピン座設定不可の図面指示をしておくと、後が楽だ。
アルミダイスカトは、注湯時に空気を逃がすために、あちこちに隙間が空いている。そこにアルミが入り込んでバリが発生する。それをプレスなどで落とすが、少しはバリが残る。それを「バリ残り」というが、思わぬところにあると他の部品と干渉したりする。なので、設計者はまず型割(パーティングライン)をしっかり把握し、干渉の恐れのある部位については、バリ残り不可または何ミリ以下などの図面指示をする。逆にどうでもよいところは、見栄えで問題にならない限り、通常のバリ残りを許容してコストを抑える。
なお、シリンダブロックについては、特に残留引張応力に対する配慮が必要だ。詳しくは「ボア変形」の中で解説しているので、そちらを参照してください。
3.樹脂部品
板金、アルミダイカストと並んでよくお目にかかるのが、樹脂部品だろう。近年、樹脂化の勢いはすごくて、軽量化やコストダウンのために、こんなものが、というものまで樹脂化が進んでいる。エアクリーナやラジエータなどは昔からだが、シリンダヘッドカバー、インテークマニホルド、フューエルデリバリパイプ、ウォータインレット/アウトレット、スロットルボデー、タイミングチェーンスプロケットなどなど、アルミや焼結に取って代わってどんどん樹脂化されている。
ただ、樹脂材は有機物質なので、基本的に経時劣化する。高温で軟化したり、給水分解したり、オゾン劣化もする。なので、使用環境にあった材料選定が非常に重要だ。
例えば、耐熱性を上げるために、ナイロン系ではグラスファイバーを添加して使うことが一般的だが(通常30%程度)、その割合が多すぎると靭性が低下する。その他、耐水性、耐油性、耐ガソリン性、耐薬品性(例えばブレーキオイル)、リサイクル性なども考慮しないといけない。なお、エンジン部品に限っては、リサイクル材ではなくバージン(新品)の樹脂材を使うことが多い。それだけ材料特性の信頼性確保に重きを置いている。そもそも、グラスファイバー入りは、リサイクル性が悪い。溶かして、成形前のペレット状にしたときに、ファイバーが切れてしまうからだ。
余談になるが、グラスファイバーは英語ではfiberglass、それなのにガラス強化ナイロンの材質表示は、PA66-GF30(66ナイロン、グラスファイバー30%の意味)などと書く。どうでもいいことだが、ちょっと不思議。
樹脂材は金属に比べて柔らかいので、基本的にボルト座面にはカラーを挿入してヘタリを防止する。フェノール系はカラーなしでもほとんどヘタリがないが、締め付け時に割れるリスクは高くなる。
樹脂材は比重が小さく、剛性も低いので、カバー類に使用する時は、リブを配置したり曲面化をして、剛性を上げるのが基本だ。シール面には通常ゴムのパッキンを組み込むが、2層成形といって、硬い樹脂のシール面に柔らかい樹脂を一体成形してゴムを廃止する方法なども、コストダウンのために開発されている。
エンジン部品に使われる主な樹脂材について、詳しくは仕入先に聞くなり材料部門に問い合わせてもらうとして、筆者の経験から、個人的見解をワンポイント解説する(間違っているかも知れません)。
材料記号 |
材料名 |
特徴 |
ABS |
エービーエス |
最も低グレードで耐熱性、耐候性も低くエンジンではほとんど使わない |
PP |
ポリプロピレン |
成形性がよく柔らかい、カバー、ケース類など強度を必要としない部位によく使われる |
PA6
PA66 |
6ナイロン
66ナイロン |
インテークマニホルド、ラジエータなどの水系にも多用されている、靭性は高く少々ねじっても簡単には折れない、グラスファイバー添加で耐熱性、強度を上げることが可能 |
PPS |
ピーピーエス |
熱に強く硬くて丈夫、ただし割れやすい |
PEEK |
ヒーク |
スーパーエンプラの最上級グレードで、高温強度は抜群だがコストがべらぼうに高い、スカイラインのターボインペラに使用されたこともある |
PF |
フェノール樹脂
(ベークライト) |
唯一熱硬化性、高温下では溶けずに炭化する
衝撃には弱いが灰皿にも使うくらい熱には強い、用途はオイルフィラキャップなどに限られる |
4.ゴム部品
樹脂同様、基本的に経時劣化するので、材料選定が非常に重要。
ゴムの製造工程は、まず原料を計量し、混練りと呼ばれるミキシング工程を経て(この段階ではゴムの弾性は全くない、柔らかい粘度のような感じ)、射出またはプレスで成形、その後、加硫(加熱)によってゴム弾性が生まれる。加硫とは、ゴム材に含まれるイオウが過熱されることで分子間に橋を架け(架橋)、それによってゴム弾性が生まれることをいう。加硫は自然環境下でも引き続き進むので、長い年月が経つとゴムはだんだん固くなり、遂にはボリボリと欠けるような状態になる。イオウを含まないゴム材もあり、それは長年使用しても硬化しにくいのが特徴。
シール材に用いる場合、常に圧縮されていることでヘタリ(永久変形)が生じ、次第に面圧が低下し漏れに至る。なので、基本的にシール材は定期交換が必要だ。また、空気に触れていることでオゾン劣化(酸素によって分解して、クラックが入る)もする。従って、シール対象(オイルと空気、水と空気、オイルと水、オイル同士、水同市、空気同士など)によって、材料の選定を変える。
オイルや冷却水で膨潤(周囲の成分を吸い込んで膨らむ)したり収縮(ゴム材の成分の一部が溶け出して縮む)する場合もある。基本的にはゴムはヘタって行くので、少しだけ膨潤するようにブレンドして、シール性を改善する方法もある。これをオイル膨潤タイプとか水膨潤タイプと呼ぶ。
一定の圧縮率で圧縮し、熱劣化やオイル劣化などをさせた後開放して、どれくらい形状が変形したかを調べる。圧縮代に対する永久ひずみの割合を、圧縮永久ひずみ率(ヘタリ率)という。勿論小さいほうがいいのだが、シール材は圧力によって変形しリークを防ぐ構造にもなっているので、ケースバイケースでむやみに高いグレードのゴムを使う必要はない。余談になるが、ゴムは温度が上がるとわずかに膨張する。勿論柔らかくもなる。なので、Oリングからの水漏れやオイル漏れは、冷機時(エンジンが冷え切った状態)に起きることが圧倒的に多い。
もうひとつ気を付けてほしいのは、ゴムは非圧縮性だということだ。つまり、圧縮しても、形状変化はするが体積変化はしない。逃げ場のない空間に閉じ込めてしまうと、部品同士の隙間を締め切ることが出来ず、浮き上がった状態になる。なので、Oリングシールの充填率は何%以下などの推奨値がある。製品のバラツキを考慮して100%を超えないような配慮が必要だ。
ゴムは交換部品だとは言っても、交換サイクルまでは異常が起きないような耐久性を確保する必要がある。その評価で重要なことは、リアルな環境(実際に取り付けられる環境)で長時間行うこと。供試ゴムそのものも、削り出しなどは不可で、量産時と同じ条件(勿論金型)で生産したものでないといけない。これらの条件が異なると異なった結果が出ることは、過去の不具合事例から学んだ教訓だ。実際現役時代には、数ヶ月単位の評価をお願いしたことも多い。エンジニアリングには、あくまでリアリティを追求する精神が大切だと思う。
ダンパー部品もゴムを使用するが、数あるゴムの中で、なぜか天然ゴム(NR)が最も温度依存性の小さい(温度変化に対してバネ定数の変化が少ない)と仕入先から聞いた。耐熱性など他の物性では合成ゴムには敵わないので、使用部位は限られるかも知れないが、狙いの周波数の許容範囲が小さい時は使用することになるので、記憶に留めておいてください。
エンジンで用いる代表的なゴム材は、NBR(主にオイル系)、EPDM(主に水系)、アクリル系、シリコン系、フッ素系(耐熱性は最上級)、NR(主にダンパ類)など非常に多種に渡るので、ひとつひとつの紹介は割愛する。代表的なゴム部品メーカー(例えばNOK)などにお願いすれば、物性表くらいはもらえると思う。
5.アルミ鋳物
アルミダイカストは基本中子は使用しないが、アンダーカット(外側から抜くことが出来ない部位)のあるピストン、シリンダヘッド、インテークマニホルドなどは、中子を使用し、溶湯を取鍋(とりべ)などで供給する方法で鋳込む。いろいろな方法があるが、総称して、アルミ鋳物と呼ぶ。
ピストンは、いわゆる重力鋳造で、鋳砂ではなく分解できる金型で中子を形成する。アルミの溶湯が固まったら、真ん中の型を抜き、左右の金型を中央に寄せて抜くことで、アンダーカットの成形が可能になる。鋳造欠陥は許されない重要部品なので、時には製品よりも大きな押湯をつける。押湯とは、アルミが固まる時に内部のアルミが収縮した分を、外の大きな湯溜まりから供給して、ヒケ巣を防止する方法。ダイカストと違って空気の巻き込みはほとんどないので、これでほぼ欠陥のないワークが出来る。
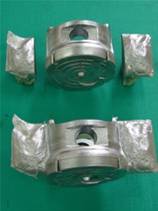
押湯
更に強度を必要とする特殊なエンジンでは、溶湯鍛造という工法がある。これは凝固の最終段階で加圧して、高温強度を高める方法。この場合は、型で押さないといけないので、アンダーカットの形状は作れない。
シリンダヘッドは、燃焼室とカム室の間に、冷却水を流すウォータージャケットという空間があるため、どうしても中子(鋳砂を固めたもの)を使わないといけない。メーカーで異なると思うが、左右前後と燃焼室側の外型は金型で、カム室とウォータージャケットに中子を用いるのが一般的か。
ウォータージャケットの形状は複雑怪奇で、中子が金型で成形出来なければならない上に(アンダーカット不可)、生産時に中子が折れないような配慮や砂残りがないような工夫も必要、勿論燃焼室をしっかり冷却出来ることなど、制約条件が鬼のようにあるので、その設計はまさに設計者の腕の見せ所だ。
代表的な鋳造方法としては、空気の巻き込みをなくすため、型の下面からエアー圧で注湯する、低圧鋳造と呼ばれる工法を用いる。
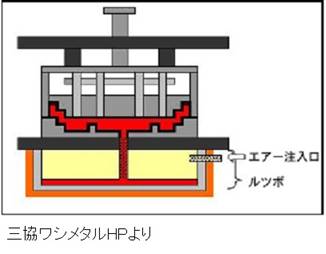
空気の巻き込みが不可なのは、勿論リークの問題もあるが、最近のシリダヘッドは、高温強度や硬度、粘り性を向上させるために熱処理をするのが一般的だからだ。粗材が空気を含むと、熱処理時に空気が膨張し(ブリスター)、製品が不良になってしまう。高出力化が進んだことで、熱処理なしの設計が難しくなって来ている事情もある。
シリンダヘッドのダイカスト化(中子レス)はエンジニアの夢だが、確かまだ一部でしか実現していないと思う。基本的にダイカストはアンダーカットが不可なので、シリンダヘッドを分割する必要があり、信頼性が確保しづらい面もある。
インテークマニホルドは一般的に湾曲しているので、傾斜鋳造という方法を用いる。
図がなくてわかりづらいと思うが、垂直に立てた型に注湯した後、型全体を傾けて、溶湯を型内に行き渡らせる方法。
勿論、直管のようなインテークマニホルドがあれば、この方法を選択する必要はないが、スペース効率から湾曲形状になるのは必至で、レーシングカーでもない限り、ストレートなインテークマニホルドは見たことがない。
6.鍛造
エンジン部品で鍛造品といえば、クランクシャフトやコンロッドがその代表選手だが、こちらは刀鍛冶や蹄鉄づくりと同じ熱間鍛造だ。
熱間鍛造とは、読んで字のごとく、鋼材を真っ赤になるまで加熱し、柔らかくなった状態で、ハンマー(無論ハンドではなく、そう呼ばれる加工機がある)やプレスで叩いて成形するもの。ハンマーは、余りに大きな音と振動があるので、筆者が見学したメーカーでは、加工機全体を水に浮かせていた。それが一般的かどうかは知見がないが、とにかくすさまじい音がするし、そばにいると恐怖感すら覚える。ここでは事故は許されないが(死ぬ、もしくは身体の一部を失う)、ワークをハンド器具でつかんで裏返したり型内を移動させたりする工程もあって、熟練が必要だ。一般的に一発で形が決まることは少なく、型同士がぶつかるまで何度か叩く。まさに鍛冶屋のイメージだ。
プレスの場合は、複数の型があって、それぞれのつぶし代が決まっている。型ごとに一発ずつ叩き、型間はトランスファーマシンで搬送する。鋼材はどんどん冷えていくので、温度や加工時間の管理が重要になる。途中で停止するようなことがあれば、その時仕掛かっているワークはすべて廃棄となる。
何しろバラツキの出やすい加工方法なので、形状を100%出そうとすると、はみ出し量をそれなりに取らないといけない。なので、粗材には大きなバリが出る、クランクシャフトは加工したときに取れる部分が多いが、コンロッドは外形は加工しないので、プレスでバリを落とした後、疲労破壊の起点とならないようショット処理をするのが一般的。「疲労破壊のメカニズム」でも触れたが、圧縮残留応力を与える狙いもある。
ボルトや小物は冷間鍛造で作る。熱間鍛造と同じように、通常はバリが発生するが、はみ出しの全くない密閉鍛造をという工法では、バリ取り工程を省略することができる。そのためには、鍛造前の粗材(例えば丸棒)を精密に軽量する必要があり、多すぎると型が破壊し、少なすぎると欠肉して不良品になる。
冷間鍛造品で重要なのは、フローが切れていないこと。切れていると内部で破断が起きていることになる。
実は鋼材には方向性があり(それがフロー)、方向によって強度が異なる。フローの方向に強く、その直角方向に弱い。なので、強度確保のためには、フローが切断されるような加工は極力避けた方がよい。板が圧延されたり、線材が引き抜き加工でしごかれたりする時に、鋼材のフローが出来ると考えている。フローのイメージは、下図を参照してください。
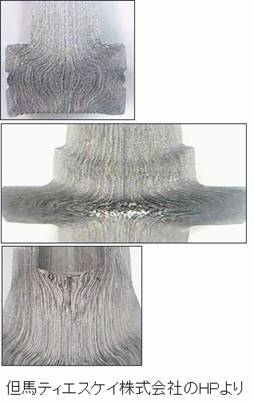
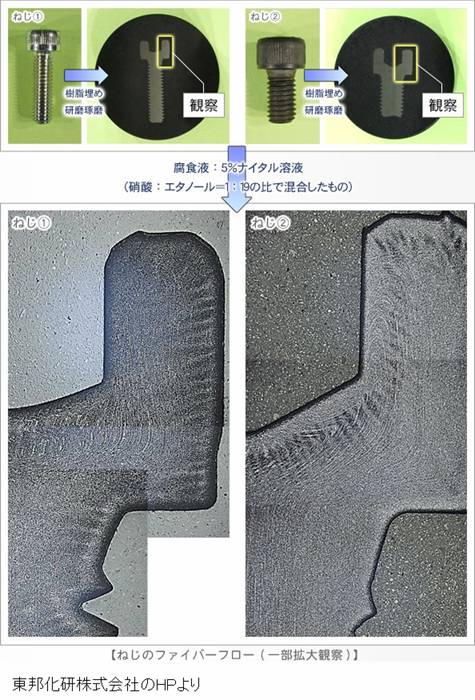
実は板金も鋼材なので、せん断面と破断面の話の中で、せん断面と呼んでいる部位は、フローが切れていない(材料が塑性変形して流れている)部分になる。
冷間鍛造は、基本的に平たい製品は苦手で、縦長の部品によく用いられるが、最近はプレス鍛造といって、少々面積のある物でも冷間で成形出来るようになってきた。ただし、使える材料は限られる。
ボルトの成形のイメージは、丸棒を定寸に切り、型に押し込んでしごき、頭の部分を叩いてつぶす、というもの。たいていは6〜8工程くらいあって、ものすごいスピードで型の中を移動して行く。
ちなみに、ボルトのねじ部はローラ転造で成形する。試作品のボルトは切削(ダイス加工、旋盤)で作る場合もあると思うが、フローが切れていて転造より強度が低くなるので、評価に関しては要注意だ。
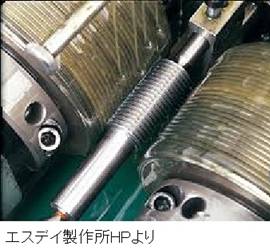
7.機械加工
機械加工は理解が容易で、あまり解説するニーズもないと思う。
普段あまり接することのないものだけ、少しご紹介しておこう。
シリンダ内面は、ホーニングという工程で仕上げる。ホーニングマシンには、シリンダ内面側に砥石が付いていて、外向きに力をかけた状態で、回転しながら上下に動く。なので、斜めにクロスした傷(クロスハッチ)が付く。クロスハッチの目的は、オイルを保持しして、ピストンやピストンリングの焼き付きを防止することだ。あまり多くのオイルを保持すると、燃焼ガスによって燃え、オイル消費が悪化する。少なすぎると焼き付く。なおかつ、使用過程で摩耗して、状態が変化する。そんなこんなで、適正なクロスハッチの角度や深さ、ピッチなどを決めるのは容易ではない。ここに各カーメーカーのノウハウが凝縮されていて、変更するには相当な勇気がいる。それでも、フリクションの低減や信頼性の向上のため、日夜研究が進んでいる。クロスハッチ角を部位によって変える、などという高等な技術も一部で採用されていて、パテントにもなっている。
ノックピン、ピストンピンなどの外形仕上げには、センタレス研磨という工法が用いられる。ミクロンオーダーの外径精度と真直度を要求される部品は、たいていセンタレス研磨だ。その加工イメージを見てもらえば、なぜそうなのかが理解できると思う。
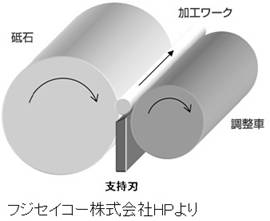
加工に関して、最後にひとつだけ、貫通穴や貫通ネジ穴に関する注意事項を書いておこう。
貫通穴や貫通ネジ穴は、図面(モデル)では何の懸念もなく描けるが、出来上がった製品を見ると、抜けた先で片当たりしていることがある。ドリルやタップが片当たりすると、折れたり精度が悪くなったりする。
それを防ぐには、製品のバラツキを考慮しても片当たりしないよう、粗材形状で逃げておくことだ。
また貫通穴や貫通ネジ穴は、一般的にはその深さを指示しないと思うが、加工のバラツキや粗材のバラツキで、更に奥の部位が削れたり、タップが入り切らず不完全ネジ部が出来たりすることがある。
それを防ぐには、貫通部位であっても、どこまでドリルを入れるかを指示したり、タップの先端がどこまで入るかを事前に調べておくのがよい。
8.鋳鉄
最近、鋳鉄製の部品はめっきり少なくなった。砂型が必要で生産性が悪い上に、重い。錆びやすい。今では、エキゾーストマニホルドとクランクシャフトの一部くらいしか残っていない。
ということで、筆者にもあまり知見がなく、かつ材質の話はモロに企業秘密に属するので、解説できる内容がほとんどない。
ひとつだけ、将来を託す若い設計者には、是非金型鋳造にチャレンジしてもらいたい。これはエンジニアの夢で(当たり前だが、普通に金型で鋳込むと、型とワークがくっついてしまう)、これが実現すれば、鋳鉄の生産性が画期的に上がり、どんどん縮小している鋳鉄の活用範囲が広がるかも知れない。ただし、エンジン向けの用途としては、主にクランクダンパの錘部分などだとは思うが。
以上、エンジン部品で使われる材料について、基本的なことだが教わる機会が少ないと思われる(筆者がそう思う)ものについて、出来るだけわかりやすく解説したつもりだ。
何度も言うが、わからないことはそのままにしないで、とにかく聞く、調べる、を是非心がけてほしい。みなさんの活躍に期待しています。
|