自動車に限らず、工業製品は簡単に壊れてはいけないという使命を背負っている。自動車は、壊れ方によっては生命の危険を伴うので尚更だ。その中でもエンジンは、動かなくなると全く走れず、路上故障不具合としてカウントされるため、市場で何件か発生しただけでリコールになる可能性もある大変責任の重いパーツだ。ただ現実にはエンジンのリコールは極めて少なく、各メーカー共それだけエンジンの信頼性の確保には力を入れている。
信頼性の問題には、ものが壊れるという以外にもいろいろな事象があるが、ここでは疲労破壊について、その考え方を出来るだけわかりやすく解説する。エンジン設計者のみならず、エンジニアとして必ず知っておかなければならない「疲労限度線図」について、理解を深めてほしいからだ。特にエンジン部品は、簡単に疲労限度の回数(鉄鋼で10,000,000回)の応力を受けるので、しょっちゅうお世話になる。大学で一度習っているはずだが、入社時にはぼくも頭に入っていなかった。とても基本的で重要な知識なので、イマイチ覚えていないという人は是非読んでください。
1.一発破壊と疲労破壊
エンジンで一発破壊という現象は、異常燃焼とハンマくらいしかない。ハンマには、ウォータハンマ、燃料ハンマがあるが、実際にあるとすればウォータハンマだ。これは、深い水たまりに突っ込んでしまって、吸気口から水を吸い込み、非圧縮性の液体である水を圧縮しようとして、コンロッドが曲がるか折れるかする現象だ。そんな試験をする意味はないので、車両側でよほどのことがない限り水が入らないようにしてある。
一方、疲労破壊は繰り返し応力がかかることで、じわじわと壊れていく現象で、エンジン部品が壊れる時は、ほとんどがこれだ。一般的に、新車で起きる不具合を初期故障型、経年車で起きる不具合を摩耗故障型というが、疲労破壊は摩耗故障型とは限らない。というのも、4気筒4サイクルエンジンが6000rpmで回転している時、疲労限度の回数(10,000,000回)に達するのに、14時間足らずしかかからないからだ。これは、爆発1次で計算しているが、共振などでもっと周波数の高い応力がかかる場合は、あっという間に壊れる。疲労破壊をなめてはいけない。
2.応力発生の要因
エンジン周りに取り付けられている部品の応力発生の要因は、エンジン振動や冷熱サイクルなどだが、爆発力と往復慣性力(ピストン系とコンロッド小端部)は打ち消しあう方向に作用するので、全負荷(フルスロットル)と無負荷(レーシング)のどちらがエンジンの振動が大きいかと言うと、一般的には無負荷の方が大きい。なので、エンジン周りに取り付けられている部品の応力測定では、必ず無負荷条件を含むようにしている。全負荷条件は、主に熱的な影響や摩耗関係でシビアな評価になるが、振動に関しては厳しいとは言えない。ただし、これはガソリンエンジンの場合で、ディーゼルエンジンは爆発力と慣性力の比率がガソリンエンジンとは異なるので、様子が違うはずだ(筆者に知見がない)。冷熱サイクルによる熱応力の影響を評価するには、全負荷運転と強制冷却を繰り返すパターン運転を行う。なお、回転慣性力(コンロッド大端部)は、クランクシャフトのカウンタウェイトでキャンセル出来るので、部品精度を除いては基本的にアンバランスは発生しない。
エンジン内部の、ピストン、コンロッド、クランクシャフトなど部品には、全負荷時に大きな応力がかかるが、この測定が大変難しい。応力測定は普通、歪みゲージを張り付けてその歪みを測定し、対象部品の材質のヤング率から応力に換算する。クランクシャフトは、スリップリングという装置を経由して、直接測定が可能だが、コンロッドは高度の技術が必要で、リンク機構で外に取り出したりする。ピストンは直接測定はほぼ不可能なので、CAEに頼ることが多い。ピストンの材料であるアルミは、温度で強度が大きく変化するので、運転状態での温度を測定することが必要となるが、直接測定が難しいので硬度法(試験後の硬度低下を測定し、温度履歴を推定する方法)を用いる。計測技術はとても重要で、その進歩も著しいので、現在はピストンの温度や応力もリアルタイムに測定できるようになっているかも知れない。
最近はステンレスのエキゾーストマニホルドの採用が進んでいるが、まだ鋳物のものも多いと思う。冷熱サイクルでの熱応力が大きい部品の代表格が、シリンダヘッドの燃焼室側とエキゾーストマニホルドだ。シリンダヘッドは、最近ではほとんどが4バルブ仕様になっていて、バルブとバルブ、スパークブラグ穴とバルブとの距離が近く、冷熱繰り返して伸び縮みすることで、大きな熱応力が発生する。エキゾーストマニホルドは、温度変化が半端なく大きいので、形状もさることながら、その支持方法(エキゾーストパイプからの入力をキャンセルするために先端を支持しないといけない)が熱応力に大きく影響する。数ミリ単位で変形することもあって、拘束されながら伸びようとするために、表面に熱ヘタリによるしわが発生する場合もある。車の寿命を考えて、冷熱サイクル試験で何サイクルもたせるかが、各メーカーのノウハウになる。
3.応力振幅と平均応力
疲労破壊が発生する要因を理解してもらったところで、本題に入る。
応力の話の前に、材料の特性ついての理解が必要だ。まずは以下の応力-ひずみ線図を見てください。
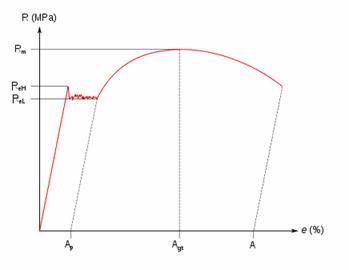
軟鋼材などの降伏点が存在する例。図中で、ReH:上降伏点、ReL:下降伏点、Rm:引張強さ、Ap:降伏点伸び、A:破断伸び。
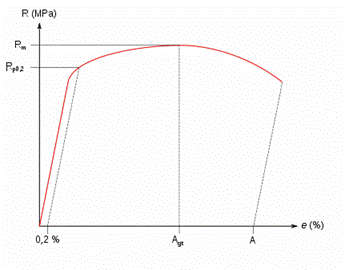
非鉄金属などの降伏点が存在しない例。図中では、 Rp0.2:0.2%耐力、Rm:引張強さ
一般的な鉄鋼材には降伏点が存在し、そこを基準に強度を考えるが、鋳物やアルミ、樹脂材には降伏点がない。更に、樹脂材は温度履歴などによって強度が低下する。ゴム材に至っては、接している相手によって膨潤したり収縮したりもする。なので、何でもかんでも同じ基準で耐久性を考えてはいけない。まずそのことを肝に銘じてください。
話はやや横道に逸れるが、ボルトの締結に関しては、実はトルクではなく軸力(ボルトが実際に引っ張っている力)が重要だ。特にヘッドボルト(シリンダヘッドとシリンダブロックを締結するボルト)やクランクキャップボルトは軸力の精度が信頼性を左右する。そこで、降伏点では伸びにかかわらず応力がほぼ一定である、という特質を利用した「降伏点締め」という工法がある。これは、降伏点ギリギリのトルクで締め上げた後、ある回転だけ更に締め上げるというもの。実際にこの工法を適用するには、相当数のテストによってその確からしさを検証する必要があるが、最近は広く採用されている。
ヘッドボルトでは更に、ボルト座面やヘッドガスケットのへたりによる軸力の低下を防ぐために、シリンダブロックのねじ部を深く追い込んで(カウンタボア)、わざとボルトの首下長さを長く取っている。シリンダブロックのねじ部が浅いと、ボルトを締め付けることでねじ部の周辺が持ち上がる現象が生じるが、それを防ぐ狙いもある。
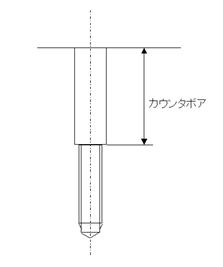
さてここからは、最もよく使われている鉄鋼材を中心に解説する。
車両部品(車体、サスペンションなど)は、走行路から不規則な入力を受けるが、エンジン部品は、比較的規則的な入力を受けることが多い。しかも、あっという間に疲労限度の回数(10,000,000回)を超えるので、熱疲労やマウント関係を除き、基本無限寿命で考える。
ここで、応力の定義をおさらいしておこう。
以下に、応力振幅と平均応力の関係を示す。
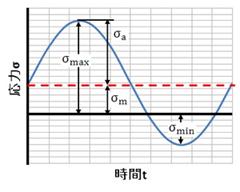
振動によって発生する応力は、一般的に両振りだが、取り付けによって初期応力が発生していることが多い。なので、応力測定は、部品がフリーの状態から始めないといけない。後で出てくるが、平均応力が耐久強度に影響するからだ。
もし耐久試験の結果と応力測定の結果が合致しない時は、応力測定の詳細をチェックしてみるとよい。測定点が最大応力点になっているか、取り付け応力の測定条件がバラツキを考慮しているか、などだ。設計者も評価の実態をしっかり把握しておくことは、とても大切なことだ。
4.疲労限度の測定方法
材料によっても異なるが、一般的な鉄鋼材には、疲労限度が存在する。ある値以下では、どれたけの回数応力を加えても破壊しない値のことだ。いわゆる無限寿命とは、応力を疲労限度以下に抑えるということになる。
そもそも疲労破壊とは、どういうものか。以下にその実態を示す。
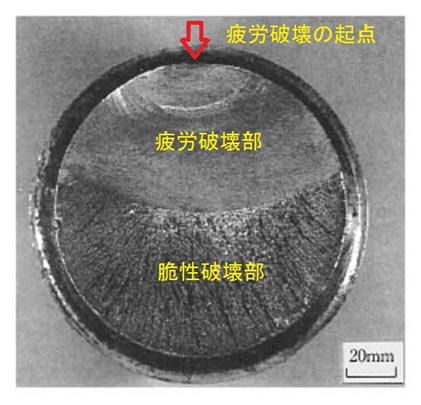
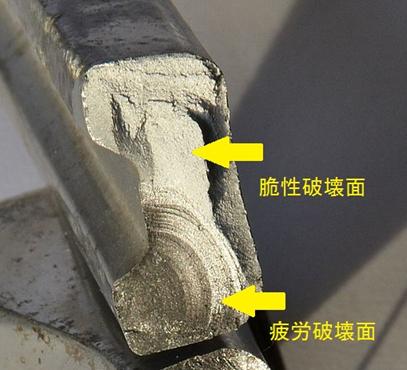
疲労破壊が起きる場合、最初に破壊が起こる起点というものがある。応力の集中している場所や、材料欠陥のある部位が多い。なので、先に結論めいたことを言ってしまうと、応力集中を避け、材料欠陥が生じにくい工法を取れば、疲労破壊を防ぐことが出来る。
それはさておき、疲労破壊は起点から徐々に進行する。ビーチマークとかストライエーションとか言われる縞模様が特徴だ。ある程度疲労破壊が進んだところで、部材が耐えられる限度を超え、最後は一気に破壊する。その部分を脆性破壊面と呼んでいる。平たく言えば、ぶっちぎれた部分だ。
設計においては、ある基準で測定された疲労限度の数値を知る必要がある。そこで、材料ごとにその値が計測されている。その方法は、テストピースに様々なレベルの一定応力をかけ、破壊までの回数をカウントすることだ。以下にそのイメージを示す(これをS-N曲線と呼んでいる、Stress Numberの略)。
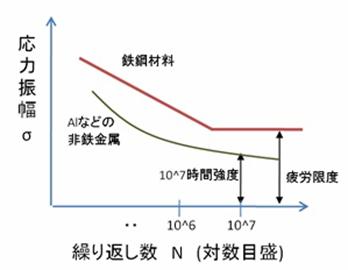
このように、鉄鋼材では、10,000,000回(10の7乗回)で、それ以上回数を増やしても破壊しない限度が存在し、それを疲労限度と呼んでいる。つまり応力を疲労限度以下に抑えれば、永久に破壊しないことになる(実際は永久というのはないと思うが)。
ちなみに、一般的な炭素鋼で疲労限度の数値は7kgf/mm2(70MPa)程度だったと記憶しているが、ネットで調べてもなかなか見つからない。唯一、国立開発研究法人物質材料研究機構が、無料でデータベースを公開しているが、設計者が使えるようなものではなかった。公称値のようなものは存在しないようだが、各カーメーカーでは設計に用いる値を持っているはずなので、社内の材料部門に問い合わせてください。
5.疲労限度線図
いよいよこの記事の最終目的である疲労限度線図を説明する。以下に示すのが、その疲労限度線図だ。
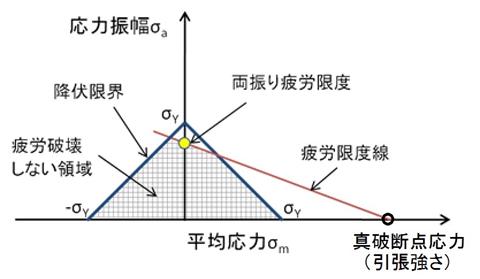
この図で、網掛け部分が使用可能範囲だ。真破断点応力とはテストピースが破断した時の荷重をその時の最小断面積で割ったもの。学術的にはこれが正しいようだが、実用的には更に安全を見て、引っ張り強さ(少し判定が厳しくなる)の値を使用する場合が多いようだ(筆者の職場では、引っ張り強さを使っていたと記憶している)。
この図の意味は、疲労限度は平均応力によって変化するもので、応力は当然それ以下に抑えなければならないが、加えて応力の最大値が降伏点を超えない、という考え方に基づいている。降伏点を超えると言うことは、物が伸びるということを意味するので、元の状態を保てないからだ。
疲労限度線の引き方は、上記以外にもいろいろあるが基本的に経験則で、すべての材料の疲労限度線を実験的に確かめている訳ではない。なので、重要な部品についてはやや過剰品質であっても厳しい側の見方をした方が後悔がない。
この図の使い方は、様々な試験条件の中で測定された最大の平均応力、応力振幅をプロットし、疲労限度線と比較する。試験自体が非常に厳しい条件で実施するので、基本的に網掛け部内にあれは破壊することはないが、重要な部品については更に測定値に安全率をかけて比較する。安全率は各メーカーのノウハウになるが、そうは言っても何倍も取ることはない。
この図では、特に平均応力が圧縮側で疲労限度の値が大きくなっていることに注目してほしい。つまり、平均応力を圧縮側にしてやれば、より安全だということになる。その考え方で、実際に行われている工法として、ショットブラストやフィレットロールがある。ショットブラストとは、金属やセラミックの粒を、部品の表面に勢いよく叩きつける工法で、表面が滑らかになり疲労破壊の起点となる表面欠陥を減らすと同時に、表面に残留圧縮応力を発生させ、応力の状態を疲労限度線図の左側にずらせる狙いがある。
フィレットロールとは、クランクシャフトに用いられる工法で、クランク軸の角に滑らかな表面のローラーを当てて加圧することで、ショットブラストよりも更に滑らかな表面を作り、残留圧縮応力も発生させる。
ここでまた少し脇道にそれて、では残留引張応力というものはあるのか。
実は、鋳造部品や樹脂部品では、当たり前のように発生する。しかも、製品が出来たときから内在するので、ひずみゲージでは測定できない。発生する原因は、溶けたものが固まる時は、基本的に縮むからだ。それなのに外形は型で強制されているから、内部で引っ張り合うしかなくなってしまう。極端な場合は、中に真空の空洞が出来る。アルミダイカストの場合、これをヒケ巣という(表面が先に固まるので、厚肉にすると出来やすい)。樹脂の場合は柔らかいので、型から離れて縮まる。これをヒケという。それを避けるには、不必要な厚肉部分を出来るだけ減らすことだ。
アルミ製のシリンダブロックでは、シリンダは鉄製のライナで構成されることが多い。この場合は、そもそもライナとアルミの注湯温度が異なるうえに、熱膨張係数もアルミは鉄の2倍ある。なので、特にシリンダとシリンダの間で大きな残留引張応力が発生する。それが燃焼による熱が加わることで解放され(なまされ)、シリンダのボアが変形する。それを防止するために、シリンダの内径を加工する前に、加熱して残留引張応力を開放しておくという工法がある。
樹脂部品では、残留引張応力に加えて、ウエルドラインという弱点部が存在する。これは、型を流れて来た2つの樹脂が合流する場所に発生する。平たく言うと、固まりかけている流れの先端部同士が、うまくくっつかないという現象だ。これはCAEもしくは評価で見つけるしかないが、ウエルドラインを発生しにくくする設計的な配慮も必要だ。

なお、残留引張応力をどうやって測定するかについては、メーカーのノウハウに当たるので紹介できないが、基本的な考え方は、その応力を別の部分を細工することで開放してやればよい、ということだ。
6.壊れにくい設計とは
最後に壊れにくい設計について解説する。
先ほど、もう答を書いてしまったが、まずは応力集中を避けること、表面欠陥の少ない形状にすることだ。更には、適正な材料や工法を選択することも重要。
最近は強度解析はほとんどCAEで実施すると思うが、CAEを過信してはいけない。境界条件や入力の方向を誤ると、間違った答が出てくるからだ。例えば、ボルトの締結部のモデル精度などは重要な要素になる。破壊が起こりやすい場所の代表が、ボルト締結部のワッシャの外周だったりするからだ。結果がおかしいと思ったら、解析の条件を見直してみるのも、問題解決のひとつの方法。CAD(Pro-E、CATIAなど)に付属している構造解析ソフトは、FEMのような細かい分解方法は取っていないので、エンジンの内部部品を扱う場合には特に注意が必要だ。計算時間はかかっても、出来るだけ現物に忠実なモデルで解析することをお勧めする。ただ、CAEでは、表面の傷や鋳造欠陥などは考慮されない。それを製造不具合と切り捨てず、部品が重なっても傷つきにくい形状とか、鋳造欠陥の出にくい設計などを心がけないといけない。
そもそも解析の前に、まず設計をする訳だが、その時点で設計者がしっかり考えていれば、後がスムースに進む。自分が設計した部品を眺めて、入力を想定した時に、壊れる場所がはっきりとわかる物は、そこから壊れる。どこから壊れるか想像がつかない形状は、第一段階として合格だ。そういう形を考えるのが設計者のセンス。
例えば、図面が書きやすいからと言って、すべての隅Rを同一にする、などというのは愚の骨頂。Rも大きければいいというものではないが(厚肉化の回避や剛性とのバランスから)、漸次変化させて応力集中を避ける工夫をするような設計者は、後が楽になる。Rの漸次変化は、別に作りにくいものではなく(ただし板金部品や素材形状の話で、加工部位はダメ)、工法を理解していればためらうこともない。ダイカストや樹脂部品では、締結点間にリブを配置するのが一般的だが、その根元に応力が集中する。そこはRを大きく取って応力を分散させるなど。
一般論として、締結点は可能であれば3点がよい(軽量化、費用対効果で)。しかも出来るだけスパンを大きく取る。4点以上では平面度の精度により、必ず取り付け応力が発生する。シール面の場合は、面圧が必要になるので、この限りにあらず。最も軽量で剛性の高い形状は、正四面体(正三角形の組み合わせ)だ。そのイメージを頭に置いて設計してみるのも、ひとつの方法。勿論、その部品に要求される機能によって、考え方は変えなくてはいけない。その上で、弱点を作らない、という基本を忘れないことだ。
設計には様々な制約があり、それを言い訳に奇妙な設計をする設計者もいるが、それはダメ。あくまで基本原理に忠実に、制約条件を見直してでも素性の良い設計を目指すのがプロです。何か、精神論になってしまいましたが・・・
適正な材料や工法を選ぶことも大切で、そのためには、材料ごとにその製造工程や欠陥の出にくい設計方法を理解していないといけない。これだけで、ひとつの大きなテーマになるので、その解説は後日に譲るが、とにかくわからないことは、社内の専門家に聞く、仕入先の技術者に聞く、文献を読む、製造現場に見に行くなど、納得できるまで調べて理解することが大切だ。急がば回れ。エンジニアたるもの、いい加減な推論や思い込みで設計をしないことです。それが、エンドユーザーに対する設計者の義務だとぼくは思います。
[添付図出典:ウィキペディア他WEBサイト]
次回は、エンジンで使われる材料の製造方法や欠陥について、その次には、信頼性確保の手法について、順次解説して行く予定です。乞う、ご期待。
|