フライホイールといえば、マニュアル・ミッション車かモーター・アシスト・タイプのハイブリッド車にしか付いていない、今時レアなエンジン部品だ。普通は鋳鉄で出来ていて、重くて頑丈。役割としては、ご存知のように、自分の慣性マスでエンジン回転を持続させて、特に低回転時に圧縮を乗り切ること(低回転以外では、回転をスムーズにして振動を押さえる働きもある)、クラッチを介してエンジンとミッションを結合したり切り離したりすること、スタータの回転をリングギヤを介してエンジンに伝えること、がある。
ところが、重い部品がクランクの後端についていることで、マイナスの面もある。
高回転で共振を起こしたりすると、振動の原因になるばかりでなく、クランクシャフトに大きな応力を発生させる。フライホイールに揺さぶられてクランクシャフトが折れることもある。
エンジンの性能試験では、トルクを吸収するダイナモに接続するために、フライホイール付きのエンジンを使う。そのことによって、エンジンの振動の様子はオートマチック車とは違ってくる。実車とベンチ(性能試験用の装置)の試験結果が異なるときに、よく問題になっていた。
オートマチック車は、フライホイールの代わりにドライブ・プレートと呼ばれるペラペラの鉄板が付いている。そのプレートにトルクコンバーターという流体継手が取り付けられていて、流体の摩擦を利用してトルクを車軸に伝える。
オートマチック車は振動・騒音がマニュアル・ミッション車に比べて良い、ということは、以前から常識になっていた。どこが違うのか。いろいろ調べている内に、どうやら、フライホイールの剛性と関係があるらしい、ということがわかって来た。フライホイールのマスを、オートマチット車のようにペラペラの鉄板の上に乗せて剛性を落としてやれば、オートマチック車並に振動・騒音が激減するのではないか。
実は、よくよく調べてみると、既にそのアイデアは世の中に発表されていた。フライホイールがたわむ構造になっているので、「フレキシブル・フライホイール」という。
振動・騒音を低減するには、エンジン側で対策する方法と、伝達系、つまり車体へ伝わることを防ぐ方法があるが、伝達系で対策した場合、どうしてもある限られた領域狙いになる。ところが、エンジン側で対策すると、もともと振動の源はエンジンなので、様々な領域で改善が可能になる。・・・と、車体の振動・騒音担当者に口説かれ、大変な開発になることを覚悟の上で、検討を始めた。
フライホイールに起因する振動は、エンジンの搭載の仕方によっては問題にならない。ただ、当時開発していた車両では、それが大きな問題となり、フレキシブル・フライホイールの成否が車両の成否を左右するとまで言われた(これは、我々をその気にさせる方便だったかも知れないが・・・)。
フレキシブル・フライホイール開発の最も重要な課題は、耐久性である。
振動・騒音については、剛性が低ければ低いほどよいというだけのことなので、如何にペラペラの鉄板で(実は、ただの鉄板では勿論ない)強度を持たせるかということになる。
もともと頑丈な鋳鉄で出来ていたものを、思いマスはそのままにペラペラの鉄板に乗せるというだけでも、大きな応力が発生する。更にクラッチを切る時の押し付け荷重を受ける。
グニャグニャと言ってもいい代物なので、低回転で共進する。その共進の仕方が半端ではない。あきれるほどたくさんのモード(揺れ方)がある。エンジンの加振力(振動させようとする力)が、こんなにバラエティに富んでいるなんて、その時あらためて認識させられた。
振動は、実は様々な周波数の成分が合成されたもので、それぞれを分解してみると、回転数の次数(何倍に当たるか、分数もある)成分になっている。グニャグニャのフライホイールは、それ自身がたくさんの共振モード(曲げ、回転、みそすり、膜振動など)を持っていて、エンジンの振動成分がそれに一致すると共振を起こす。それを変位計で実測し、モードを確定し、鉄板(以後プレートと呼ぼう)の応力を測定する。それが疲労限度を越えていたら、対策しなければならない。
この開発でのひとつの教訓は、一言で言うと「柳に風」である。
応力は力任せに対策すると剛性を上げる方向に向かう。振動・騒音は悪化し、更に応力が増し、他の部品にまでそれが及ぶ。
ここでは、プレートの板厚は変えず、応力集中を避ける「柳に風」作戦を取る。
余談になるが、筆者は常々こう言っている。
どこから壊れるか予想が付くものは、必ずそこから壊れる。予想がつかないようにしてしまうことで、重量やコストを増やさずに対策できる。応力集中をなくし、バランスを取る、ということだ。始めから予想が出来ない人は、いろいろ経験をして、感性を磨く必要があるが・・・
今回もこれで行く。
開発が始まった頃、ドライブ・プレートに関してノウハウを持っている部品メーカーが、プレートの全面にクラッチ板冷却用の穴を開けた、本当にグニャグニャの案を持ってきた。筆者はそれを見た瞬間に絶句し、これはダメです、と言ったが、メーカーは更にCAE解析結果を持参し、自信たっぷりに、強度は持つと断言した。それでも自分の感性がNOと叫んでいた筆者は、メーカー案と冷却穴をすべて埋めた筆者の案を両方試作することにした。
しばらくして、実験部署から電話があり、現場に呼び出された。何とメーカー案の試作品はレーシングをしただけで破壊したという。ブレートは引きちぎられて、フライホイール本体がバウジングに干渉し、飛び出す寸前までハウジングをえぐっていたが、幸い外には飛び出さず、犠牲者を出さずに済んだ。
メーカー案の試作品は即廃却した。物には限度というものがある。筆者は、CAEはよく利用するが、その結果を鵜呑みにはしない。感性というものが重要である、といういい事例になった。
クラッチ板の冷却については、ハウジングを工夫することで解決した。
ところで、肝心の応力集中の方は、どうやって解決したか。
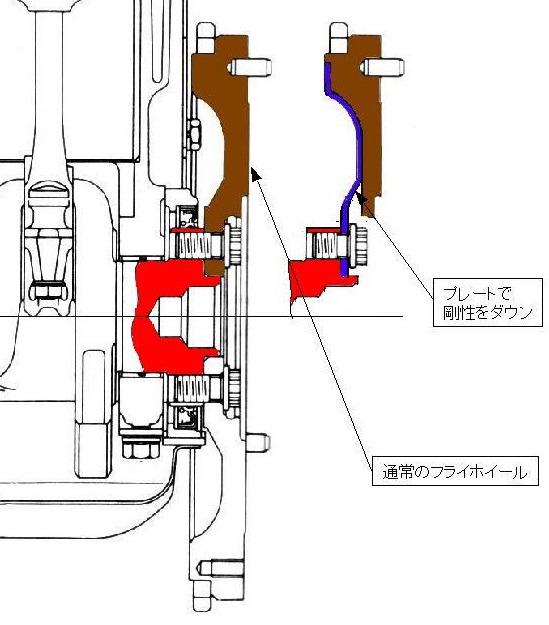
フレキシブルフライホイールの断面図
上図を見ていただくと一目瞭然だが、応力は小さな曲率で曲げられる部分に集中する。
すなわち、クランクシャフトと接する面の端、取り付けボルト周り、その2点である。クランクシャフトもボルトも共通品なので、それはそのまま使いたい。という訳で、それぞれ間に緩衝材(これもプレート)を挿入することで、応力緩和を図った(図は説明のためプレート挿入前の状態を示す)。
だが、もうひとつ問題がある。
磨耗である。
金属は叩かれている内に、フレッティングという現象を起こす。これは、叩かれた時に狭い隙間から逃げ遅れた酸素が、圧力によって金属と反応し酸化が進むことをいう。酸化した金属はいわゆるセラミック状になるので簡単に剥がれ落ち、磨耗が進む。
微小な振動ほど、このフレッティングは起こる。前回紹介したコンロッド合せ面にも起こり得る現象である。
この対策にはいろいろあって、耐フレッティング性の高い材料を使う方法もあるが、コスト的に有利な表面処理で対策することとした(と、サラッと説明しておきます)。
これでもまだ万全とは言えない。
新しい機構を取り入れる時に是非やっておかなければいけないのは、FMEAである。筆者はFMEAの信奉者といってもいい。常に新機構採用時にはFMEAを実施して来た。
FMEAは、Failure Mode and Effects Analysis の略で、ある欠陥なり故障が生じた時に、それがどれくらい影響が大きいかを前もって予測し、その影響の大きいものについて事前に対策しておくために実施する。
テクノロジーの世界はコストとの戦いでもある。よかれと思うことをすべてやったのでは、アポロ宇宙船の世界になってしまう。重点志向が必要だが、それには優先順位を付けること、抜けを防ぐことが肝要だ。そこで、商業化も考慮しているスペースシャトルの開発で考案されたのがFMEAだ。
FMEAには、このような部品の開発の他に、システムのFMEA、製造工程のFMEAなど、様々なものがある。
新しい技術にチャレンジする時には、品質保証の教科書を紐解いて、是非このFMEAを実施するようお勧めする。遠回りのように見えても、実は一番確かな近道だと、筆者は考えている。その際、最も大切なことは、ノウハウを持ったその道のスペシャリストを集めること、どんな意見も頭ごなしに否定しないこと、の2点だ。専門家の話を謙虚に聞く、この姿勢がないと、せっかくのFMEAもただのセレモニーになる。そして、FMEAが出来上がったら、開発の節目節目でその結果をフォローし、きちんとデザイン・レビューすること。技術屋さんは、そういう場が好きだ。自分のことでなくても、いろいろアドバイスをくれる。それをしっかり活用すること。これに尽きる。
かくして、大勢の専門家の助けを借りてフレキシブル・フライホイールは完成し、これまで一件の不具合もない。
|