1987年頃のことになるが、新エンジンの開発に携わることが出来た。エンジン設計者といえども、新しいエンジンをゼロから開発出来るチャンスはそうざらにない。高額な設備投資をして完成されたエンジンは、その後改良を重ねながら、10年15年と活用される。それだけに、最初にポテンシャルを高くして産んでおかないと、性能アップなどの改良時に苦労する羽目になる。
だから、当時、そのエンジンを開発するに当たってのコンセプトは、徹底的に信頼性の高いエンジンを作ること、そして汎用性を十分に考慮すること、であった。汎用性については、すべての車両に搭載可能なこと、すなわち、縦置き(FR)、横置き(FF)、スラント(エンジンを床下に寝かせて配置すること)が可能なアレンジをあらかじめ計画して設計された。
とにかく、筆者としては千載一遇のチャンスであったし、その当時は、毎日が新しい体験で仕事が楽しくて仕方がなかった。そのエンジン開発の楽しさを、読者に少しだけでも味わっていただきたい。そう考え、このコーナを設けた。
さて、前置きはこれくらいにして、早速本題に入ろう。
コネクティング・ロッド(連接棒・・・何と古風な呼び名)、略してコンロッドは、ピストンに加えられた爆発圧力をクランクに伝える役割を果たす、エンジン心臓部の部品である。
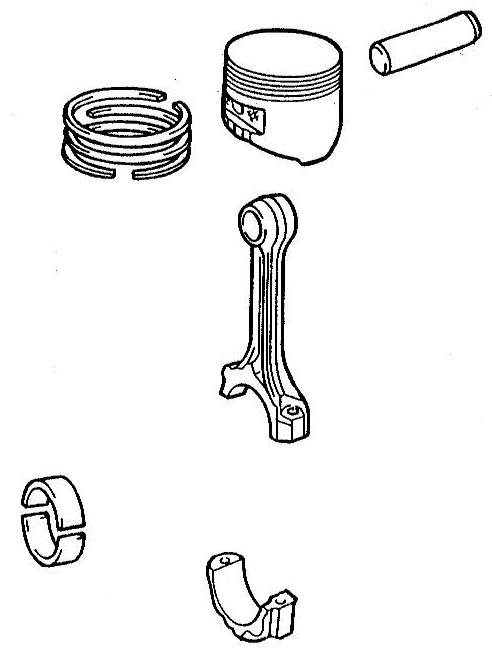
コンロッド周り部品
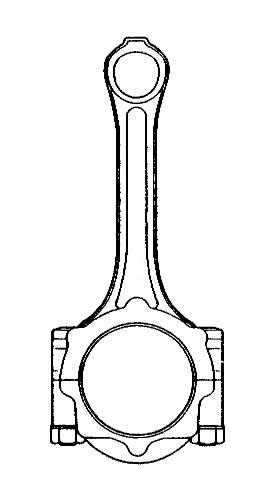
コンロッドASSY
ここではコンロッドそのものではなく、クランクに組み付けるために分割された大端部を接合するボルトについて解説する。
エンジンには無数のボルトが使われ、それぞれ重要な役割を果たしているし、それぞれ設計基準が決められている。どういう力がかかり、どんな環境で働くかによって、その締め付け方法にも色々な約束事がある。例えば、シリンダヘッドとシリンダブロックを締結するヘッドボルトは、単に爆発力に耐えればよい訳ではなく、部財の温度変化による伸縮に対応しつつ、ヘッドとブロックの間に設けられたガスケットの面圧バランスを保ち、燃焼ガスや冷却水が外部に漏れることを防がなければいけない。
それにしても、通常ボルトにかかる力といえば、引っ張り力とせん断力。コンロッドボルトの設計計算も当時はそう考えられていた。
エンジン開発が進み、耐久試験が始まったある日、コンロッドボルトが折れた。
と簡単に書いてしまったが、このボルトが折れると、コンロッドがクランクから外れ、暴れる。クランクから供給されているオイルが噴出し、油圧が一気に低下して、他のシリンダのクランクメタルが焼き付き、そのシリンダのコンロッドまで折れてしまう。折れたコンロッドはシリンダブロックの壁を突き破り、試験室は噴出したオイルが飛散してもくもくと煙に包まれる。大変な騒ぎである。勿論、無人運転しているし、消火設備も整っているから、被害は物的なものだけだが、それにしても高価な試作エンジン1台がお釈迦になる。当然、設計者が呼ばれ、原因を調べろと言われる。けれど、焼き付いたりバラバラになったエンジンを見たって何もわからない。ここから、シャーロック・ホームズばりの推理と検証が始まる。誤解を恐れずに言うと、これが実に楽しい。
通常、不具合が発生した時の解析方法としては、FTA(Fault Tree Analysis)という手法が一般的だ。我々の仲間内ではこれを「魚の骨」と呼ぶ。Treeというより、横倒しの姿で使うことが多いので、魚の骨の方がイメージに合う。
で、いろいろ考えてみる。ボルトにかかる入力を計算した結果では、疲労限度線図(解説は省略、大学の材力の講義を思い出してほしい)からの安全率は**倍もある(**は企業ノウハウに当たるので非公開、以下同様)。それじゃ何で折れるのか。
コンロッドは上下に動くだけでなく、左右に揺動する。これを我々は「むち打ち」と呼ぶ。その力なのか。いや、そんなオーダーではない。
そこで、現地現物主義を思い出し、もう一度バラバラになったエンジンの部品をかき集め、顕微鏡的ないやらしさで詳細に調査する。材質に欠陥はないか、破断面の特徴はどうか。その結果、わかったことはこうだ。
折れた2本の内、一本は一発破壊である。つまり、もう一本が折れたために、その影響で一瞬で折れた。が、もう一本はどう見ても疲労破壊。しかも疲労の起点は内側。何でそんなに大きな応力がかかるのか。どうして内側なのか。
今でもそうだが、当時筆者は野蛮人と言われていた。やることがアカデミックでない、という意味だ。で、試験担当者から、それじゃ一度引っ張ってみよう、と言われた時、そうしようと一も二もなく賛成した。
従来も、コンロッドの首部の強度試験のために、コンロッドの引っ張り試験はやっていた。今度はボルトの応力を測定するためにやろうという訳だ。ただし、今回は特殊な冶具は使わない。本物のクランクにメタルをかませて、実態に近い形で引っ張った。コンロッドボルトの疲労の起点部(内側)とその反対側(外側)には、応力測定用の歪ゲージが張りつけた。これが実に芸術的な器用さを必要とする細かい作業で、社内にはその手の達人がいた。
結果を見て驚いた。ボルトの内側と外側では応力値が**倍も違っている。でもどうして。この結果からすると、ボルトは曲がっているということなのだ。
そもそも、クランクメタルが組付けられた状態のコンロッド大端部の内径は、実は真円ではない。業界ではこれをレモンの形になぞらえて、レモン・ボアと呼んでいる(下図の青線)。
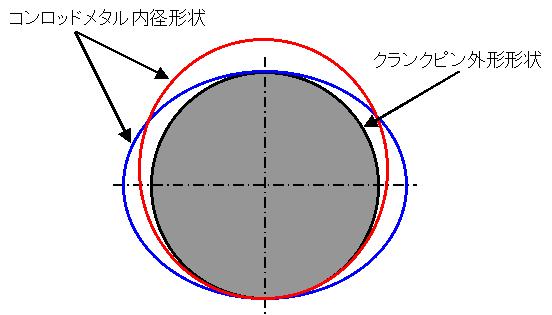
この形の意味は、「くさび型」の断面を取ることで、もっとも油圧が必要となる上下部に潤沢にオイルを供給するためである。この断面形状により、クランク軸が回転する時に、オイルを積極的に巻き込むことができる。ということは、上下より左右の方がクリアランスが大きいということになり、極端に大きな引っ張り力が働いたときは、コンロッド大端部の内径は、クランクピンに撒き付くように変形する(上図の赤線)。これが、コンロッドボルトに「曲げ」を与える原因なのだ。
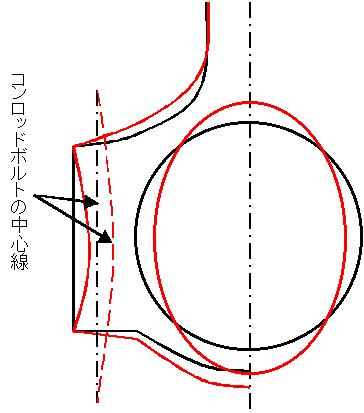
では、今までのエンジンでは起こらなかったコンロッドボルトの「曲げ」が、どうしてこのエンジンでは起こったのか。
このエンジンでは、高性能化の一環として最高回転数アップを企画した。出力は発生トルクと回転数の掛け算なので、同じトルクでも回転数が高いと大きな出力を得ることができる。レーシングカーのエンジンが1分間に何万回転という、通常の自動車用エンジンの何倍もの回転をさせるのはそのためだ。そこで問題となるのは、往復運動部と回転運動部の慣性質量である。これが大きければ大きいほどエンジンはそれに耐えるため頑丈に作る必要があり、重く大きくコストの高いものになる。また、慣性質量は振動やノイズの原因ともなる。すなわち、出来るだけ慣性質量を減らすことが、エンジンのポテンシャルを高めることになる。
そこで、このエンジンのコンロッドは徹底的に軽量化を図った。
当時、CAE(Computer Aided Engineering)が本格的に導入され始めた頃だった。特にFEM(構造解析、何の略か失念した)が盛んに活用され、それまで板要素が主だった解析がコンピュータの性能向上のおかげで3次元のMASS(中身のつまった塊)が扱えるようになり、エンジンの主用部品の設計検討に用いられた。当然、我々はFEM解析を用いてコンロッドの応力を細部に渡って予測し、あらゆる駄肉を削り取った。その結果、画期的に軽量のコンロッドが出来あがり、コンロッドそのものの耐久性は無駄のない形で確保できたが、細身になった分、剛性が落ちた。つまり、たわみやすくなった、ということだ。
これまでのコンロッドは駄肉をいっぱい付けた重いコンロッドだった。だから、ピストンの慣性力で少々引っ張られても変形は少なかった。それで、コンロッドボルトの曲げは生じなかった。今回のコンロッドはスマートになった分、しなやかになってしまったという訳だ。
理由はそれだけではない。それに加えて、新エンジンでは、絶対にこわれないエンジンを作るために、耐久試験の条件を厳しくした。耐久屋が、やたら高回転でぶんまわしてくれた。それが、更に慣性力を大きなものにした。
このふたつの理由により、それまで問題とならなかったコンロッドボルトの「曲げ」が生じたという訳だ。
対策については、原因の裏返しなので、読者の想像にお任せする。実は我々はいとも簡単な方法で対策を行ったのだが、それは企業秘密なので、ノーコメントだ。勿論、その後この不具合は起こっていない。
後で文献を調べてみると、他社で同様の事例が報告されていた。従って、コンロッドボルトが曲がる、ということ自体は既に当時からノウハウではなかった。ので、読者のみなさんに紹介することができた、という訳だ。
ここで筆者が教訓として学んだことは、いくつかあるが、まとめると以下のようなことだろうか。
1. 不具合の解析を行う時に、現物から離れて予断を行ってはいけない。ひつこく現物を調べること。そこから出発すること。
2. CAEは、それを行った視点からはある程度正しい答が得られるが、別の視点にそれを拡張することは危険だ。更に言えば、答えが感覚と全く合わないときは、境界条件をよく吟味してみるとよい。
3. 再現試験は、できるだけ現物に近い形(部品ならそのものを使う)で行うこと。それで再現しないときは、条件だけを厳しくして行くこと。冶具を使った試験は実体と合わないことが多いので、お勧めしない。
ここで、筆者が始めてCAEと出会った時の話をしよう。
先ほどの事例から更に遡ること約10年、まだ駆け出しの筆者は、ある重要な板金(鉄板をプレス成形したもの)ブラケットの設計を担当した。非常にシンプルな設計をし、何の問題もないと思っていたが、悪路耐久走行で、そのブラケットが見事に破損。最初は、試作工程で作られたための物不良と考えていたが、当時導入されたばかりのCAEを実施したところ、目からウロコの解析結果が出た。設計計算では、荷重に対する応力だけを考慮していたが、実はそのブラケットは形状の影響でよじれ、板の内外に応力のアンバランスが生じていた。対策はそのアンバランスをなくすように形状変更することだった。従って全くコストアップなしで対策することができた。わかってしまえば、単純なことだった。
物がどう変形するかは、想像するしかない。しかし、それをはっきりイメージで示し、応力も色分け表示で直感的に理解できるように表示してくれるCAEにより、具体的な対策方法の立案とその効果の確認を、相当のレベルまで机上で行えるようになった。しかも、イラストのように直感的にわかりやすいので、上司への説明も楽だ。何より、応力の分布を一目で見ることが出来、以後何度も「目からウロコ」を経験した。
CAEは設計計算に比べて、より現物的であると思う。ただ、「もろ刃の刃」なのは、境界条件を誤ると全く異なった結果が出てくることだ。境界条件こそ、現物で細かくチェックして行くしか、方法がない。急がば回れ、の世界がCAEである。
|