そもそもシリンダブロックをアルミで作ることが何故トレンドになっているのかを説明する前に、いきなりボア変形とはどういうことかと思われるかも知れないが、筆者としては、今更という気もする。
アルミ化のメリットを数えれば切りが無い。軽量化による燃費の向上、リサイクル性の高さ、暖気の早さ/冷却性の良さによる低排気ガス性(特に未燃焼成分)、鋳造時間の短さと鋳造工場の環境の良さ、加工の容易さ、寸法精度の高さ(加工の省略によるコストダウンが可能)、等々。今後、シンリダブロックの製造方法のトレンドが鋳鉄に戻ることはないだろう。
だが、勿論課題もないわけではない。特に筆者がアルミダイカスト・シリンダブロックを開発していた当時は、まだアルミか鋳鉄かという議論が真剣になされていた時代なので、技術的に解決しなければならない問題が山積していた。
その中でも、当時我々の頭を悩ましたのが、ボア変形なのだ。
ピストンの頭にはご存知の通り、燃焼ガスをシールし壁面のオイルを掻き落とすためにピストンリングがついている。ピストンリングは、燃焼ガスの圧力に負けないためとオイルの掻き残しを減らすために、面積当りの圧力(面圧)を高くする必要があるが、強い力で押し付けたのでは摩擦力が大きくなり、無駄なエネルギーを浪費(機械損失=メカニカル・ロス)してしまう。そこで、薄く薄くして、面圧だけを高くするように設計している。そうすると今度はシリンダと接する部分が磨耗して、燃焼ガスが洩れたりオイルを掻き落とせなくなる。そうならないように、ピストンリングの表面は非常に固い材料で表面処理が施されている。
一方、アルミは大変柔らかい金属である。ピストンリングの硬さには、到底歯が立たないので、シリンダの内面(ボアと呼ぶ)だけは硬度を高くする必要がある(ピストンとの焼付きを防止する意味もある)。それにはいくつかの方法があるが、最も一般的な方法はシリンダライナと呼ばれる鋳鉄の薄い円筒を、鋳造時に鋳込んでしまう方法だ。
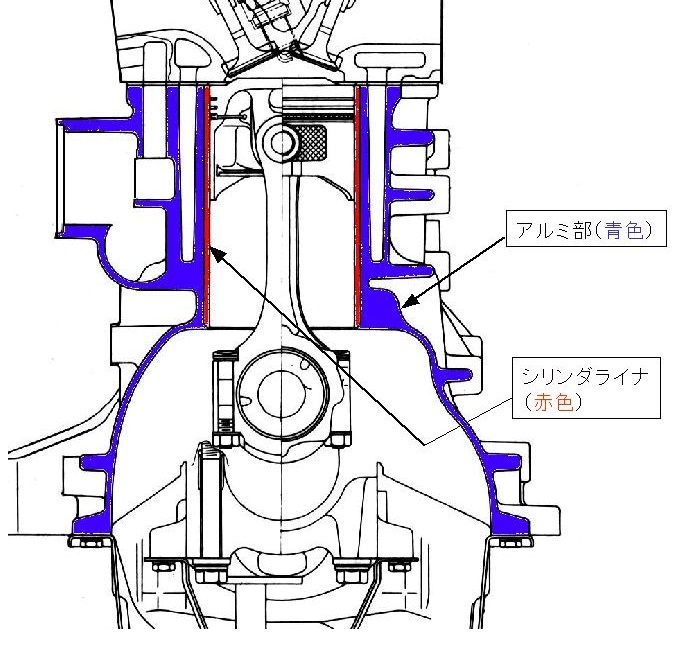
その他にも、ボアの内面にメッキ等で表面処理をする方法や、シリコン成分の多いアルミ(ハイシリコン=硬い)をライナ材として用いる方法、古くはウェットライナ(冷却水に直接接する構造なので、こう呼ばれている)のような方法もあり、それぞれ得失がある。
当時もいろいろな方法を検討したが、最終的には鋳込みライナ方式を採用することした。コストや生産性を重視した結果であるが、ここではその是非は議論せず、鋳込みライナ方式の技術的な課題を紹介したい。
鋳込みライナ方式のシリンダブロック製造方法は、以下の手順で行う。
まず、ダイカスト金型を開き、内面を洗浄する。ライナを金型に設けられたガイドに挿入して、高温になっている金型で予熱する。金型を閉じ、1平方センチ当り1トン近い圧力で溶けたアルミを注入する。一瞬でアルミは注入が終わり、冷却の工程に入る。アルミが凝固したら再び金型を開き、でき上がった素材の塊(ワーク)を取り出し水没させて冷却した後、アルミ注入のための通路(湯口)で固まった部分やバリ(型の合せ面に出る出っ張り)を切断する。素材での機密検査を行い、空気の漏れ量が設定値を超えると不良品として処分、設定以下のものを良品として後工程に送る。
全工程で数分。
この間、ライナとそれを取り巻くアルミの間に応力と変形が生じるが、そのメカニズムは以下の通りである。
アルミが凝固して冷却する際には、熱膨張係数の大きな(約2倍)のアルミの方が沢山縮もうとする。そのため、ライナはアルミから圧縮の力を受け、逆にアルミはライナから引っ張りの力を受ける。アルミ側は形状的に一様ではないため、応力の高い部分の伸びが大きくなり、そのためにライナはいびつな形に変形する。

その状態でのアルミ側の応力は、図中青の矢印で示したように、部位によって大きく異なっている。これら鋳造によって生じた内部応力を、我々は残留応力と呼んでいる。
この後、シリンダブロックは加工が施され、完成品となる。その時にも実はいろいろな外力を受けるが、その部分は省略する。
シリンダブロックはエンジン部品として組み立てられる。試運転を経て自動車に組込まれ、ユーザーの手に渡る。ドライバーは、胸躍らせながらキーをひねり、10数年、10数万キロに渡る熱と応力の耐久の履歴がスタートする。
当然、エンジンはガソリンの燃焼で力を出しているのだから、シリンダブロックは高温にさらされる。アルミは温度が上昇すると、どんどん強度が低下する。200℃程度でも、引っ張り強さはかなり落ちる。冷却水に接している部分ではアルミの温度はかなり押さえられるが、シリンダとシリンダの間には冷却水は流れない。これはエンジンの全長を出来るだけ小さくするために、シリンダ同士をくっつけてしまっているためだ。
そこでシリンダ間のアルミは高温になり、強度が落ちる。ところが、図2で示したように、この部分が最も鋳造時の残留応力が高いのだ。するとどうなるか。その通り、応力に負けてアルミが伸びてしまうのだ。その結果、アルミでぎゅっと縮められていたライナがアルミの伸びた方向に変形してしまう、これがボア変形である。
これを専門的に表現すると、熱履歴による応力緩和(クリープ)ということになる。飴が高温になるとぐにゃぐにゃになり、ある力がかかかっていると(例えば上から何かで押されていると)変形する(押しつぶされる)のをイメージしていただくとよい。
風吹けば桶屋がもうかる、くらい長〜いストーリーなので、一度では理解できないはず。極めたい人は、もう一度じっくり読み返していただきたい。極めなくていい人は、先に進まれてもよい。
ボアが変形してしまっては、冒頭に書いたピストンリングとの間に隙間が出来て、燃焼ガスが洩れたり、オイルが掻き切れずオイル消費が悪化するのではないか。
そのことで頭を悩ました我々技術陣は、とにかくホア変形のメカニズムの究明とその対策に日々奮闘した訳である。
従来からボア変形については、ある基準があった。シリンダブロックとシリンダヘッドをボルトで締め付けた時、それだけでボアに変形が生じる。エンジン屋さんは経験的にそのときの変形量の上限を決めている。
ところが今回のボア変形は、一桁違うくらいの大きな変形量だったのだ。
会社のトップもあわてた。我々に檄が飛んだ。
けれども我々は思った。待て待て、先人の例がある。それを調べてみよう。言わすもがな、先人とはH社さんである。
解体屋を訪ねて、出来るだけ古いエンジンを探した。解体屋が変な顔をしていた。何でそんな古いボロボロのエンジンを、嬉しそうな顔をして買って帰るのかと。
そのエンジンは、シリンダが4連ではなく、2連と2連に分かれていた。まあ、少々の違いはいい、と、タリロンド(真円度計)で測定して、驚いた。そのシリンダも、物の見事に変形していて、しかも値もほとんど同レベルだったのだ。
いろいろ調べている内に、問題は変形の大きさではなく、その様態であることがわかった。鋳鉄ブロックのボルトを締め付けた時のボア変形は、細かく波打っている。けれども、アルミブロックの変形は、値は大きいが緩やかで、ほとんど楕円のような形になっている。逆にアルミブロックでは、シリンダはボルトとは切り離されていて、締め付けによる変形がない。従って、ピストンリングはボアに追従してくれて、燃焼ガス洩れもオイル掻き落とし不足も起こらないというわけだ。
ただし変形量が半端ではないから、ピストンの形状やピストンリングの仕様については、それを十分考慮しなければいけない。
という事で、結論を言うと、ボア変形ありきで、周りのスペックを決めて行った。それにより、当時としてはオイル消費も大変少なく、同時に摺動抵抗も小さい(即ち燃費のよい)スペックにまとめることが出来た。
トップに叱咤激励に耐え、何とかノーマルな形で量産出来たことで、みんな胸を撫で下ろした。
実はボア変形では、もう1点、ガスシールの問題があった。鋳造時に変形したライナを加工すると、どうしても肉厚にバラツキがでる。その薄いところを狙ってガスが洩れる。
だがこの問題を説明すると長くなるし、重要なノウハウをたくさん含んでいる。
公開出来ない内容が多すぎて、何を言っているのかわからなくなるので、残念ながら割愛させていただく。
ここでの教訓は、設計基準というものは、単なる数字ではいけないということだ。
設計基準は法律でも道徳でもない。そこに技術的な理由があって決められている。そのバックグラウンドを知らずに盲信すれば、今回のアルミブロックは量産出来なかった。
会社のトップは当然細かな技術的背景はご存知なく、その数字を見て大変心配された。毎日のように検討結果をフォローされた。開発責任者としてのその気持ちは十分理解できる。ただ、数字だけを議論していたら、アルミブロックは完成しなかった。
この頃、大企業の中では、決まり事、基準、数字だけが一人歩きするような現象は起きていないだろうか。
公式や基準は覚えなくていい。その生まれた訳を理解していれば。と、筆者は思う。
我々は技術者であって、役人ではない(公務員の方、ごめんなさい)。ルールを守っていればいい、という考えでは、新技術は生まれない。
現地現物。しっかり現象を捉え、実態を見て、考え抜く姿勢を持ちたいものだ。
|