耐火物
GHIJKLMNOPQR 古川邦男
1、まえがき
鉄鋼プロセスの進歩は、それに合った耐火物の開発に支えられてきたといっても過言ではない。
一般に使用条件の過酷になる新プロセスに、耐火物は材質の開発、施工技術、使用技術、補修技術などの開発改善によって対処してきた。これらの現状について述べ、そして今後についても一緒に考えてみたい。
2、耐火物とは
2ー1 耐火物の定義 *1、2
1700〜1800℃の高温によく耐える非金属材料を耐火材料(refractory
materials)と呼び、使用 に具合の良いように形状を整えたものを耐火煉瓦(refractory bricks)と称している。
ゼーゲルコーン26番(SK26)以上のものを耐火物と呼ぶ定義もあるが(JIS
2002)、現在では『高温で 使用できる材料』位が一般的である。また、建設材料関係で耐火材料と呼んでいるものもあるが、耐熱温度も1000℃位であり、防火材料(fire-proof
materials)と呼ぶべきである。また、耐熱材料というものもあるが、耐火物と同等に扱ってもよい。この中には、耐熱ガラスや耐熱合金も含まれる。
2ー2 耐火物の分類
耐火物の分類法には種々の分け方がされているが、化学成分による分類と形態による分類について述べる。
@化学成分による分類
表1:耐火物の化学成分による分類
|
|
分類 |
種類 |
化学成分 |
酸性
|
SiO2系 |
珪石煉瓦、溶融石英煉瓦 |
SiO2 |
Al2O3系 |
アルミナ煉瓦、高アルミナ煉瓦 |
Al2O3 |
Al2O3-SiO2系 |
ロー石煉瓦、シャモット煉瓦 |
Al2O3、SiO2 |
ZrO2系 |
ジルコン煉瓦、ジルコニア煉瓦 |
ZrO2・SiO2、 ZrO2 |
MgO系 |
マグネシア煉瓦 |
MgO |
MgO-Cr2O3系 |
マグクロ煉瓦 |
MgO-Cr2O3 |
MgO-CaO系 |
ドロマイト煉瓦 |
MgO-CaO |
MgO-Al2O3系 |
スピネル煉瓦 |
MgO・Al2O3 |
非酸化物
|
C系 |
カーボン煉瓦 |
C |
SiC系 |
炭化硅素煉瓦 |
SiC、C |
SiC-C系 |
炭化硅素ーカーボン煉瓦 |
SiC、C |
SiC-Si3N4系 |
炭化硅素ー窒化硅素煉瓦 |
SiC、Si3N4 |
複合系 |
MgO-C系 |
マグネシアカーボン煉瓦 |
MgO、C |
Al2O3-C系 |
アルミナカーボン煉瓦 |
Al2O3、C |
Al2O3-SiC-C系 |
炭化硅素含有煉瓦 |
Al2O3,SiC、C | |
A形態による分類
表2:耐火物の形態による分類
分類 |
具体例 |
分類 |
具体例 |
定形煉瓦
|
アルミナ煉瓦 カーボンブロック SNノズル 浸漬ノズル 断熱煉瓦 ポーラス煉瓦 |
不定形耐火物
|
キャスタブル モルタル 吹き付け材 圧入材 スタンプ材 溶射材 |
ファイバー |
アルミナ繊維 |
2ー3 耐火物の生産
耐火物の生産量は鉄の生産量に結びついている。図1に日本の年度別の粗鋼生産量を示す。*3
平成2年度(バブルの絶頂期)をピークに減少の傾向を示し、平成4、5年度は1億トンを割っている。
しかしながら、この3年間は連続して1億トンを越えている。
図2に日本の耐火物の生産量の変化を示す。*4
図1:粗鋼生産量の変化
図2:耐火物の生産量の変化
耐火物の生産量は年々減少の傾向を示す。また減少しているのは定形煉瓦であり、不定形耐火物の生産量の変化は小さい。すなわち、不定形化比率が増加していることを意味している。平成4年度で不定形耐火物
の生産量が定型耐火物のそれを越えた。耐火物の生産量の減少は、主として製鉄所サイドの耐火物原単価が低下したことによる。今後、さらに製鉄メーカーの国際価格購買政策の進行により、輸入煉瓦の使用量が増加し、国内生産量の減少が続くものと考えられる。
図3に耐火物の用途を示す。耐火物の用途の約63%は鉄鋼向けであることがわかる。
図3:耐火物の用途 *4
2ー4 耐火物の原料
耐火物の原料には天然原料と人造原料がある。また、輸入品も多く使用され、1995年度では原料消費量の
38.6%が輸入原料である。また、人工合成原料は35.3%を占めている。*5
表3:原料の例
|
天然原料 |
人造原料 |
国産 |
ロー石、粘土、珪石
|
アルミナセメント、合成ムライト 焼結アルミナ、電融アルミナ |
輸入原料 |
クロム鉱、シリマナイト 礬土頁岩、ジルコン、黒鉛 |
炭化硅素、電融アルミナ 電融マグネシア、アルミナセメント、 |
2ー5 耐火物の物性とその評価
耐火物は @製造工程での製造管理、品質管理、A製品の基本特性と応用特性、B製品のシュミレーション試
験、C製品の実炉試験などの種々の試験が実施される。表4に耐火物の特性例を示す。
表4:耐火物の主な特性値
|
分類 |
特性 |
測定の目的 |
基礎特性
|
化学組成 、鉱物組成 |
耐火物の基礎組成を知る。 |
組織観察(顕微鏡、EPMAなど) |
組織を知り、構造設計の情報を得る。 |
比重、気孔率 |
煉瓦の基礎特性 |
通気率 |
耐火物への通気性。スラグの浸透性などを知る。 |
細孔分布 |
細孔の分布を知り、浸透、爆裂性向の指標。 |
圧縮強さ |
強度の指標 |
曲げ強さ |
強度の指標 |
弾性率 |
耐熱衝撃性推定に使用、熱応力の計算に使用 |
耐火度 |
熱効果の指標で、熱効果下での溶融温度 |
荷重軟化温度 |
荷重下での変形開始温度 |
熱間曲げ強さ |
熱間での強度 |
熱伝導率 |
伝熱計算の基礎データー |
熱膨張率 |
熱応力の計算基礎、競りの推定 |
応用特性
|
浸食試験(耐スラグ性、耐メタル性) |
実使用時に接触する反応性物質に対する抵抗 |
耐熱衝撃性(熱スポーリング性) |
急熱急冷に対する特性 |
耐酸化性 |
最近多い含炭素材料の酸化に対する抵抗 |
耐磨耗性 |
機械的衝撃、流動溶融体下での磨耗特性評価 |
施工性 |
不定形耐火物の施工特性。流動性、硬化時間など。 |
耐爆裂性 |
不定形耐火物の乾燥時の水蒸気爆発への抵抗性 | |
さらに多くの評価法があるが基本的なものに留めた。耐火物の使用条件は非常に複雑であり、いくつかの特性の組み合わせで実使用との相関を推定できることは少ない。従って、実使用に近いシュミーレターを製作し評価試験されることが多い。しかし、実際は実炉で使用しないと本当のことがわからないと言っても過言でない。
3、製鋼用耐火物の使用の実際
3ー1 溶銑鍋、混銑車
@ 溶銑鍋
溶銑鍋用耐火物は、本邦で多量産出する蝋石主体とした蝋石煉瓦が主体であったが、近年溶銑鍋が、脱燐 や脱硫処理の容器として使用されるために、耐食性に優れ、耐構造スポーリング性に優れ、さらに、スラグ浸透が小さく耐食性に優れるAl2O3-SiC-C質煉瓦が使用されるようになった。最近は煉瓦に代わり、不定形の流し込み施工が行われている例もある。表5に溶銑鍋用耐火物の例を示す。*5
表5:溶銑鍋用耐火物の例
|
|
A |
B |
C |
D |
|
煉瓦 |
キャスタブル |
化学成分 (%)
|
Al2O3 |
68.5 |
70.0 |
65.5 |
76.5 |
SiO2 |
5.0 |
3.8 |
8.3 |
2.2 |
SiC |
7.5 |
14.6 |
14.6 |
14.6 |
C |
6.3 |
6.9 |
6.8 |
3.0 |
MgO |
1.9 |
|
|
|
嵩比重 100℃×24H |
2.80 |
2.86 |
2.81 |
2.97 |
見掛気孔率(%) 100℃×24H |
13.0 |
13.0 |
13.5 |
14.5 |
圧縮強さ(Mpa) 100℃×24H |
4.6 |
2.7 |
2.5 |
2.0 |
残存膨張率(%) 1500℃×3H |
+0.2 |
-0.1 |
+0.4 |
+0.1 |
熱間曲げ強さ(Mpa)1400℃×1H |
0.9 |
0.28 |
1.96 |
0.35 |
浸食比 1500℃×1H C/S=2.4 |
100 |
108 |
116 |
95 | |
図4:混銑車のライニングの例*10
A 混銑車
図4に混銑車のライニングを、表5に煉瓦の品質例を示す。*7溶銑の運搬容器の場合は、高級シャモット煉瓦が主体であるが、脱硫処理が始まると、スラグライン部の先行溶損を防止するために、高アルミナ煉瓦が使用されるようになり、さらに脱硅・脱燐・脱硫の溶銑予備処理が行われるようになり、耐用性の高いAl2O3-SiC-C質煉瓦が使用されるように
なった。Al2O3-SiC-C質煉瓦の耐食性に及ぼす影響としては、アルミナ骨材はSi02量が少なく、黒鉛量が多いほど*8、また黒鉛粒度が微細なほど耐食性に優れている。*9 表5に混銑車用煉瓦の特性例を示す。
表5:混銑車用煉瓦の特性例
|
材質 |
高級粘土質(焼成) |
高アルミナ質煉瓦(焼成) |
Al2O3-SiC-C質 |
MgO-C(不焼成)質 |
受銑口キャスタブル |
嵩比重 |
2.35 |
2.64 |
2.78 |
2.83 |
2.30 |
見掛気孔率(%) |
12.5 |
17.5 |
11.2 |
3.7 |
22.0 |
圧縮強さ (Mpa) |
88.3 |
103.0 |
52.0 |
36.3 |
65.7 |
曲げ強さ (Mpa) |
常温 |
21.5 |
17.6 |
22.6 |
17.6 |
14.7 |
At
1400℃ |
2.94 |
5.88 |
5.09 |
3.92 |
1.96 |
熱膨張率 (%) At 1000℃ |
0.55 |
0.52 |
0.48 |
1.00 |
0.53 |
化学成分 (%)
|
SiO2 |
53 |
22 |
7 |
|
32 |
Al2O3 |
42 |
75 |
59 |
|
60 |
SiC |
|
|
18 |
MgO
78 |
|
C |
|
|
10 |
20 |
|
備考 |
内張り一般 |
スラグライン、受銑口 耐食性、耐スポール性 |
高アルミナにSIC,C 耐食性、耐スポール |
マグネシア原料にCを添 加、 耐食性 |
1500℃×
3Hの 測定値 | |
B 溶銑予備処理
溶銑鍋や混銑車で溶銑予備処理を兼用する方法に対して、一方専用
炉を使用する報告がある。
図5に溶銑予備処理の概略フローシートを示す。*1
従来の
MgO煉瓦に比較して溶損速度が26%減少した。これら専用
炉は固有の特性があり、それに合った耐火物の開発が必要である。
図5:溶銑予備処理の概略
3ー2 転炉
1979年に転炉への MgO-C
煉瓦の適応が開始されるまでは、転炉煉瓦の主流はマグネシア・ドロマイト煉瓦であった。現在では転炉のほとんどの部位に使用されている。MgO-C煉瓦は、マグネシア原料とカーボンから構成されている。マグネシア原料は転炉のCaO/SiO2比の高いスラグに対して優れた耐食性を示すが、高い熱膨張のために、熱衝撃に弱い性質を持っている。これにカーボンを配することによって、煉瓦の熱膨張を押さえ、また熱伝導率を高めることによって熱スポーリング抵抗が向上する。また、カーボンはスラグの浸透を防止し、また冷却効果を高め耐食性を向上する。*11 表6に転炉用煉瓦の特性例を示す。
転炉煉瓦の損耗は部位によって異なるが、一般的な壁の損耗は、カーボンの酸化により、酸化層にスラグが浸透し、溶損されることと、熱スポーリングによって剥離が発生ことであるといわれている。図6にカーボンの浸透防止効果を示す。図7にスラグのMgO含有量とそのスラグへの煉瓦成分のMgOの溶解傾向を示す。また、図8はスラグコーティングの効果を示す。すなわち、スラグのMgO含有量を制御し、スラグコーティングを施すことによって炉寿命の延長を図ることができることを示している。近年、スラグスプッラシュコティング法の導入も行われ、さらに転炉の寿命延長に貢献している。
表6 転炉用 MgO-C煉瓦の特性例
|
PTGA15F-3 |
PHS-20A |
PHA-20A |
PHA-20F |
QHD-20F |
嵩比重 |
2.88 |
2.96 |
2.90 |
2.86 |
2.83 |
見掛気孔率(%) |
3.5 |
1.6 |
3.0 |
3.0 |
3.0 |
圧縮強さ(Mpa) |
47.0
|
38.2 |
34.3 |
34.3 |
34.3 |
荷重軟化温度(2s/p2
) |
≧ 1700
℃ |
≧
1700 |
≧
1700 |
≧
1700 |
≧
1700 |
曲げ強さ 1200℃ |
13.7
|
ー |
15.2 |
14.2 |
13.7 |
(Mpa) 1400℃ |
11.2 |
13.2 |
14.2 |
13.2 |
170 |
化学組成 (%) |
MgO
C SiC |
76 14 3 |
75 21 |
75 21 |
74
21 |
76
20 |
特徴
|
耐酸化性 耐食性 |
耐熱スポール性 耐食性 |
耐食性 高温安定性 |
耐食性 高温安定性 |
耐食性 高温安定性 |
用途
|
転炉炉口 傾斜部
|
炉底羽口 CBノズル 炉底スリーブ |
トラニオン 出鋼口
|
トラニオン 出鋼壁 傾斜部 炉底 |
トラニオン 傾斜部 炉底 |
系 |
MgO-SiC-C |
焼結マグ |
電融マグ |
焼結マグ |
高純度焼結マグ |
図6:カーボンの効果
図7スラグ中のMgOの影響 図8:スラグコート量の影響
3ー3 溶鋼鍋 *14〜19
溶鋼鍋の内張り材料は、長年煉瓦が用いられてきたが、築炉の省力化、作業環境の改善、原単価の低減を目的として不定形化が開始され、種々の施工法が用いられてきたが、現在は流し込み施工が主流になっている。不定形化の初期には蝋石や珪石を主体としたものであったが、鋼品質の高級化により使用条件が過酷化し、一般壁には、主にアルミナーマグネシア質または一部アルミナースピネル質が使用されている。敷には、アルミナースピネル質が、スラグラインには
MgO-C質煉瓦、または
MgOーZrO2ーSiO2質、アルミナーマグネシア質、MgO-CaO質などの流し込み材が使用されている。表7に鋼鍋用の不定形材の代表物性を示す。
表7鋼鍋溶不定形材の例
使用部位 |
一般壁 、 敷 |
スラグライン |
材 質 |
アルミナースピネル質 |
アルミナーマグネシア質 |
マグネシアージルコニア質 |
化学 組成 (%) |
Al2O3 |
91.6 |
88.1 |
ー |
MgO |
6.0 |
6.7 |
83.8 |
ZrO2 |
ー |
ー |
7.5 |
乾 燥 後 |
嵩比重 |
3.04 |
3.05 |
2.91 |
気孔率 ( % ) |
16.4 |
17.5 |
16.4 |
曲げ強さ(MPa) |
7.0 |
9.4 |
10.3 |
図9に流し込み施工の様子を示す。
流し込みで施工された鋳込体は数時間で 図9 取鍋の流し込み施工
硬化する。脱型後乾燥され、ライニングが完成する。予熱後、受鋼に
供される。
鋼鍋の使用での溶損はスラグラインは化学的な
侵食が主であるが、一般壁は剥離による損耗
が支配的になる。同様に敷は、溶鋼の落下の
衝撃や剥離で損耗する。
3ー4 二次精錬
@真空脱ガス処理*20
鋼の真空脱ガス処理を行うプロセスには種々存在するが、圧延用鋼材等の大量生産に対応するプロセスとしては、DH脱ガス法とRH脱ガス法が
主力である。これらの装置は脱水素処理だけでなく、脱炭、脱硫、成分制御、さらに酸素吹き込みにより、溶鋼の昇熱、極低炭素鋼の溶製、フラックスの吹き込みによる極低硫鋼の溶製、ステンレス鋼の溶製等、精錬機能の充実・拡大が進み、もはや単なる脱ガス装置ではなく、多機能な反応装置になってき ている。
図10にRH法を、そして図11にDH法の概略図を示す。*21
図10 RH設備
(左図)
図11 DH設備
(右図)
これらの装置に使用される耐火物は、真空下の特殊な条件で使用される。それゆえ、真空下で安定であること、溶鋼の環流による磨耗作用に耐えること、耐熱スポーリング性に優れていること、さらにスラグ、フラックス、および高温のFe-oxideに対して優れた耐食性が要求される。*22〜24 現在、主に使用される内張り材はマグクロ質ダイレクトボンド煉瓦、電融マグクロ原料を使用したセミリボンド煉瓦やリボンド煉瓦が用いられている。表8に代表的な内張り材を示す。
表8 真空脱ガス用耐火物
|
|
DBH-5 |
H-6U |
C-6UA |
H-F1U |
C-F1U |
SRC-SHA |
SRC-SHB |
特徴 |
耐スポーリング性 |
○〜◎ |
○ |
○ |
△ |
〜△ |
〜△ |
〜△ |
熱間強度 |
〜△ |
〜△ |
△ |
〜○ |
△ |
○〜◎ |
◎ |
耐食性 |
〜△ |
〜○ |
△〜○ |
○ |
○〜◎ |
○〜◎ |
◎ |
化 学 組 成 (%) |
SiO2 |
1.9 |
1.7 |
1.4 |
1.9 |
1.4 |
2.1 |
2.4 |
Al2O3 |
8.9 |
8.8 |
5.6 |
10.3 |
5.6 |
7.1 |
8.9 |
Fe2O3 |
4.4 |
4.3 |
4.6 |
7.3 |
7.2 |
9.3 |
9.7 |
CaO |
0.6 |
0.6 |
0.5 |
0.4 |
0.3 |
0.5 |
0.6 |
MgO |
72.3 |
71.6 |
71.0 |
55.2 |
53.9 |
52.3 |
54.0 |
Cr2O3 |
11.2 |
13.6 |
16.4 |
23.7 |
31.4 |
28.7 |
24.5 |
物
性
|
見掛比重 |
3.64 |
3.65 |
3.69 |
3.80 |
3.85 |
3.88 |
3.85 |
かさ比重 |
3.06 |
3.13 |
3.16 |
3.19 |
3.22 |
3.51 |
3.47 |
見掛気孔率 (%) |
16.0 |
14.2 |
14.4 |
15.9 |
16.2 |
9.6 |
9.9 |
圧縮強さ(Mpa) |
52.9 |
70.1 |
61.7 |
52.5 |
49.0 |
119 |
1321 |
熱間曲げ強さ Mpa |
RT |
6.3 |
8.3 |
6
3 |
9.3 |
7.8 |
14.7 |
24.0 |
200℃ |
12.2 |
18.1 |
14.2 |
20.1 |
14.7 |
34.3 |
39.2 |
500℃ |
3.9 |
7.4 |
4.9 |
7.8 |
6.4 |
11.3 |
16.7 |
|
|
|
|
|
|
|
|
熱スポーリング試験 1600℃ →RT |
亀裂発生回数 |
1〜2 |
1〜2 |
1 |
1 |
1 |
1 |
1 |
剥落回数
|
27
|
23
|
24
|
12
|
12
|
9
|
6
|
浸食比 数字が小ほど良好 |
100 |
68 |
62 |
45 |
41 |
26 |
26 | |
A その他の精錬
Aー1 電気炉*25
電気炉は従来の交流式から、直流式に代わりつつある。また、出鋼方式も従来の出鋼樋から、炉底から出 鋼するEBT方式(eccentric
bottom
tapping)や底吹き法のガス攪拌の技術も導入されている。電気炉用耐火物は炉蓋、炉壁の水冷化の大幅な普及や取鍋精錬の採用で現在は溶鋼の接触する側壁下部や炉底部を残のみとなった。
Aー2 取鍋精錬炉 *26
取鍋精錬炉はASEA−SKF,VAF,LF等があるが、この中で優れた機能、および作業性を持つL Fが急激に増加し我が国の取鍋精錬炉の大部分を占めている。LFは従来の加熱装置を持たない真空脱ガス法では処理中の溶鋼温度の低下が弱点であったが、この温度低下をアーク加熱でカバーし、取鍋中の溶鋼を積極的に精錬できるようにしたものである。
3ー5 造塊
@タンディシュ
タンディシュに主に使用される耐火物は、一般の壁のライニング、羽口、堰、コーティング材である。
一般壁のライニングの材料には蝋石、中アルミナ質、高アルミナ質の煉瓦または不定形材料(流し込み)が 使用されている。堰は溶鋼中の非金属介在物を除去するために使用されるもので、中アルミナまたは高アルミ ナ質のプレキャストキャスタブルが使用されている。一部非金属介在物の吸収能力の高い石灰質の堰が使用されている。コーテイング材は固化した残鋼を除去し易いようにタンディシュ表面に塗布されるもので、これから非金属介在物が鋼に入らないようにMgO質の材料の使用が一般的である、また堰と同様、石灰質のものもある。当然、最近増えつつある熱間回転タンディシュではコーティング材は使用されない。
A連続鋳造
近年、日本においては連続鋳造技術の進歩にともない適応鋼種の拡大、多連鋳化、高速鋳造等、そこで使用される耐火物に対する要求はますます過酷化してきており、機能用耐火物と呼ばれる所以である。連続鋳造用として用いられる耐火物は機能別に各種様々であるが(図12)*27 、ここでは特にスライディングノズルプレート、ロングノズル、イマージョンノズル等について概説する。
図12 連続鋳造用耐火物 図13 スライディングノズル用耐火物の変遷
(1) スライディングノズル
スライディングノズルは取鍋、およびタンディシュの流量制御用に用いられ、要求される特性としては、溶鋼流に対
する高耐食性、高耐熱衝撃性等が必要*28である。図13*28に材質の変遷を示す。現在はピッチ含浸高アル
ミナから無発煙タイプのAl2O3−C質が主流になっている。表9に材質の例を示す。
(2) ロングノズル 及び
イマージョンノズル
ロングノズルは取鍋とタンディシュの間にあって溶鋼流の酸化や乱流の防止、流量の制御の役割を担っている。また、イマージョンノズルはロングノズルと同様に無酸化鋳造を目的に使用されるが、溶鋼吐出流の制御による介
在物の浮上促進やモールドパウダーの巻き込み防止などの重要な役割を果たしている。
これらの具備条件は、
(1)高温下での高強度
(2)溶鋼、スラグ、モールドパウダー等に対する高耐食性、耐摩耗性
(3)急激な温度変化によって生じる耐熱衝撃性 である。
(2)-1 ロングノズル
無予熱の溶融シリカ質に変わる物として、Al2O3-SiO2-Graphite質*30が、低熱膨張、Graphiteの高熱伝 導性のため使用されている。CおよびSiO2の添加は耐熱衝撃性を向上させるが、耐食性を低下させるので、いずれも30%以下で使用される*31,32。ロングノズルの割れは鋼の断気の続行が出来なくなることから、耐食性と耐スポール性のバランスが材質選定のキーポイントになる。*33
(2)-2 イマージョンノズル
イマージョンノズルの本体を構成するAl2O3-(SiO2)-Graphite質についてはロングノズルと重複するので、以下には
モルタルパウダーと接する部位に使用される、及びアルミナの付着抑制方法等について述べる。
1、パ゚ウダーライン材質*34,35
モールドパウダー
に接触するパウダーラインが溶損ネック部位になる。パウダー成分にはアルカリ成分や弗
素を含み低粘性である。現在は、ZrO2-Graphite質がパウダーライン部のみに使用されている。
2,アルミナ付着防止*36〜38
付着防止には a)脱酸生成物の粘性を下げる。b)溶鋼の清浄
c)ノズル内へのAr吹き込み
d)溶鋼温度の低下の抑制
e)ノズル界面の低融化 などがある。e)については、ZrO2-CaO-Graph-
ite質がよいという報告がある。表10に物性の代表例を示す。
表9 スライディングノズルの代表物性値
|
材質名 |
A-Z-S-C |
Al2O3−
ZrO2−C |
Al2O3− ZrO2 |
MgO-C |
A |
B |
C |
D |
E |
F |
品質 |
嵩比重 |
3.06 |
3.23 |
3.30 |
3.25 |
3.45 |
3.06 |
見掛気孔率(%) |
7.3 |
6.8 |
5.8 |
4.8 |
9.0 |
5.1 |
圧縮強さ(Mpa) |
168 |
167 |
187 |
211 |
233 |
149 |
曲げ強さ (Mpa) |
RT |
28.4 |
30.5 |
30.1 |
31.7 |
31.1 |
31.4 |
1400℃ |
24.5 |
26.0 |
25.7 |
27.2 |
10.1 |
31.1 |
化学成分 (%)
|
SiO2 |
4.0 |
|
|
|
0.4 |
|
Al2O3 |
65.5 |
76.4 |
72.0 |
70.4 |
90.1 |
MgO 93.5 |
ZrO2 |
11.1 |
9.9 |
13.0 |
12.8 |
7.0 |
|
SiC |
5.1 |
2.3 |
2.4 |
2.9 |
|
|
C |
12.8 |
9.2 |
10.5 |
12.2 |
2.2 |
3.4 |
耐食性 指数 |
100 |
40 |
42 |
48 |
38 |
15 小がよい |
耐スポール性 |
亀裂発生時間 |
29 sec |
24 |
34 |
38 |
24 |
17 |
亀裂の程度 |
○ |
○ |
○〜◎ |
◎ |
○ |
○〜△ | |
a) から e)を組み合わせた対策がとられることが多い。
表10 ロングノズル、イマージョンノズルの物性例
|
ロングノズル |
イマージョンノズル |
付着防止 |
|
A |
B |
C |
D |
E |
F |
G |
H |
I |
化 学 成 分 (%) |
SiO2 |
25 |
27 |
27 |
|
5 |
5 |
|
|
文献 *38 |
Al2O3 |
43 |
42 |
42 |
63 |
67 |
74 |
|
|
ZrO2 |
|
|
|
|
|
|
70 |
76 |
50 |
CaO |
|
|
|
|
|
|
5 |
4 |
21 |
C |
32 |
31 |
31 |
31 |
27 |
20 |
20 |
18 |
27 |
品
質 |
嵩比重 |
2.20 |
2.18 |
2.21 |
2.54 |
2.54 |
2.60 |
3.40 |
3.52 |
2.87 |
見掛気孔率(%) |
14.3 |
15.8 |
14.8 |
16.8 |
16.5 |
16.9 |
14.2 |
13.5 |
15.0 |
圧縮強さ(Mpa) |
27.5
|
27.4 |
30.3 |
26.3 |
24.5 |
28.2 |
|
|
24.5 |
曲げ強さ At RT |
10.3 |
11.2 |
11.5 |
9.2
|
8.3 |
7.8
|
10.2 |
10.6 |
10.2 |
(Mpa) 1400℃ |
9.1
|
10.8 |
11.3 |
10.5 |
8.3
|
7.4 |
9.2 |
9.6 |
9.8 |
弾性率×104 (Mpa) |
0.98 |
1.06 |
1.28 |
0.98 |
0.78 |
1.32 |
|
|
|
熱膨張率 At 1000℃ (α)% |
0.27 |
0.2 |
0.25 |
0.42 |
0.38 |
0.40 |
0.38 |
0.40 |
|
耐スポール指数 |
Sλ/Eα |
508 |
570 |
496 |
360 |
336 |
111 |
|
|
|
比率 |
100 |
112 |
98 |
71 |
66 |
22 |
|
|
|
溶損比 (ラボ) |
154 |
61 |
63 |
46 |
59 |
36 |
100 |
67 |
|
熱伝導率 〔W/(m・K)〕(λ) |
16.3 |
16.3
|
16.3
|
16.3
|
14.0 |
9.3 |
|
|
|
ΔTスポーリング試験
|
1000
℃ |
◎ |
◎ |
◎ |
◎ |
◎ |
600
◎ |
|
1200
℃ |
◎ |
◎ |
◎ |
◎ |
◎ |
800
× |
1400
℃ |
◎ |
◎ |
◎ |
○〜△ |
○〜△ |
|
1500
℃ |
◎ |
◎ |
○〜△ |
|
× |
|
1550
℃ |
○ |
◎ |
|
|
|
|
3ー6 補修装置と材料
実際の炉では、最初にライニングされた耐火物が、使われ始めた後、そのまま最後まで使用されることはない。炉は使用途中でどこかに何かの欠陥(亀裂、剥離など)が発生する。そのまま放置すると、その局所のみ が原因で炉が寿命を迎える。これは、他の部分は大量の耐火物を残すことになり不経済である。また、現実的に、その欠陥から湯漏れでも起こせば大変なことになる。従って、炉は何らかの方法によって補修される。補 修には種々のケースがあり、吹き付け、パッティング、焼付、圧入、流し込み、溶射など、それぞれに合った種々の 方法が考案され実用されている。ここでは、代表的な4種類について述べる。
@吹き付け補修 *39,40
粉末状、またはスラリー状の粉末を吹き付け機で吹き付ける方法で、簡便であり、施工技術の修得が容易である。施工は従来の冷間が主流であったが、冷却によるエネルギー損失が無視出来ず、現在はほとんどが熱間である。吹き付け材の難しい点は、施工時の水分許容幅を広くすること、施工温度の幅の広い中で、十分な接着性が得られ、一定の時間で硬化させることの制御、急速な温度上昇時に爆裂しないこと、そして十分な耐食
性の確保等、一見矛盾する条件をバランスよく満足させることである。
表11に吹き付け材の特性例を、図14に施工例を示す。
A焼き付け補修 *41,42
表11 吹き付け材と焼き付け材の物性例
材料を熱間の炉に直接投げ込み、材 料の溶融による流動性を利用して被施 工面に焼き付ける。流動性を与える結 合材には、ピッチ、あるいはフェノー ルレジンが一般的である。簡便に大量 処理ができ、耐用性は吹き付けより優 れるが、垂直部の施工ができないことと、大量のガスの発生で環境に悪いと いう欠点を持っている。 表11に材料の特性例を、図15に 施工の実際例を示す。
| |
|
吹き付け材 |
焼付材 |
材 質 |
塩基性 |
中性 |
塩基性 |
塩基性 |
成 分 |
マグアル |
アルミナ |
ASC |
MgO-C |
結合材 |
燐酸塩 |
セメント |
セメント |
カーボン |
使用場所 |
溶鋼鍋 |
RH |
溶銑樋 |
転炉 |
化 学
分
|
Al2O3 |
23.6 |
94.6 |
71.7 |
|
CaO |
2.6 |
3.2 |
3.0 |
0.8 |
SiO2 |
5.4 |
0.1 |
13.6 |
|
MgO |
63.2 |
|
|
73.2 |
SiC |
|
|
8.1 |
7.3 |
C |
|
|
|
|
嵩比重 |
100℃×24Hr |
2.26 |
2.37 |
2.52 |
1.97 |
500℃× 3Hr |
2.23 |
2.24 |
2.51 |
2.14 |
曲げ強さ 100℃×24Hr |
1.0 |
2.9 |
3.0 |
5.9 |
(Mpa)1500℃× 3Hr |
3.2 |
4.0 |
8.2 |
3.2 |
熱間曲げ強さ (Mpa) 1400℃×1Hr |
0.2 |
1.2 |
1.0 |
5.6 | |
図14 吹き付け施工 図15 焼き付け施工
B圧入施工
枠のある個所に、短時間に大量の材料を圧入する。
熱間、冷間の両方がある。表12に代表特性を示し、図16に施工を示す。圧送パイプ内で十分な流動性を与えるために、水と耐火物の粉末が分離しないように保水性を与えること、接着性に優れること、熱間施工の場合、耐爆裂を有することが、配合設計ポイントになる。
表12 圧入材の特性例
図16 圧入補修のシステム
|
|
水系 |
非水系 |
|
Al2O3-MgO |
Al2O3-Spinel |
MgO |
化学組成 (%) |
Al2O3 |
87.5 |
87.8 |
|
MgO |
9.7 |
9.8 |
85.0 |
C |
|
|
4.5 |
1550℃焼成後 線変化率(%) |
1.05 |
1.02 |
0.56 |
曲げ強さ(MPa) |
18.3 |
16.8 |
22.3 |
圧縮強さ(MPa) |
28.5 |
29.0 |
34 |
見掛気孔率(%) |
29.8 |
31.5 |
25 |
熱間曲げ(MPa)1000℃ |
2.58 |
2.46 |
2.45 |
混練水分(%) |
10.5 |
10.7 |
|
特徴
|
高強度 耐スラグ性
|
高強度 耐
Fe2O3 性
|
高強度 接着性 耐食性 | |
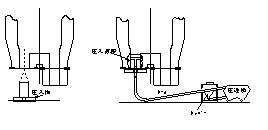
図17 溶射補修のシステム
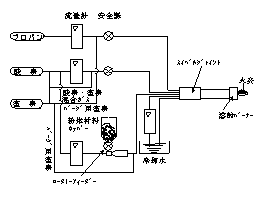
| |
C溶射補修 *43,44,45、46
特殊なバーナーから噴射、溶融された耐火粉末を、窯炉内張ライニングの損傷部位に接着させる熱間補修法のことで、究極の吹き付け施工ともいえる。表13に溶射補修技術の特徴を示す。耐用性は従来法に比べて抜群であるが、設備費のイニシャルコストが高いとか、材料が特殊になり、やや高価になるという問題点はあるが、現在日本の製鉄所での普及は大である。
表14に材料特性例を、図15に実用結果を示す。
符号 |
LFMPL-3 |
LFAM-1 |
LFAR-30 |
|
適応炉 |
補修部耐用性 炉の寿命 |
|
材質 |
MgO-CaO |
アルースピ |
アルミナークロム |
溶射 |
吹付 |
溶射 |
吹付 |
化 学 組 成 |
MgO CaO Al2O3 Cr2O3 Fe2O3 SiO2 |
60 % 22
9
5 |
8
90
1 |
9
84 4 1 1 |
ガス炉 RH,DH 吸上管) |
15
ch |
3 ch
以下 |
90
ch |
75
ch |
転 炉 |
普通鋼 |
20 |
3〜4
ch |
2300ch |
1400ch |
ステンレス |
4 |
1
ch以下 |
内130ch |
内
60ch |
取鍋 |
10
ch |
1
ch以下 |
50
ch |
40
ch |
溶射 後 品質 |
見掛気孔率(%) 見掛比重 嵩比重 |
4.8 3.49 3.36 |
22.7 3.67 2.84 |
25.8 3.79 2.81 |
熱風炉 |
8年以上 |
1.5年 |
15年以上 |
15年 |
↑ 表14 溶射補修の実用例(上)
← 表15 溶射材料の特性例 (左) |
適 応 炉 |
転炉 脱ガス炉 取鍋 |
◎
○ ○ |
◎ ◎ |
◎ ◎ |
表13 溶射補修技術の特徴
|
|
施工方法 |
適応炉 |
問題点と対策 |
水 と 耐 火 物 に よ る 補 修
|
冷 間 補 修
|
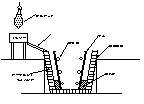
流し込み補修 |
溶銑鍋 溶鋼鍋
|
(問題点) (対策) (理想的な対応技術) |
|
|
熱ロス大 |
|
間補 |
|
火
炎
溶
射
補
修
技
術 |
|
|
|
納期大 |
|
容量化 |
|
|
|
|
熱 間 補 修 |
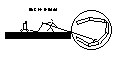
吹き付け補修 |
高炉 転炉 脱ガス炉 加熱炉 |
|
耐用性小 |
|
|
施工体の 緻密化 |
|
|
|
|
炉壁温度 低 下 |
|
|
|
|
|
|
付着性小 |
|
付着率 向 上 |
|
部分的 な交換 補修
|
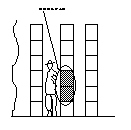
|
溶銑鍋 溶鋼鍋 転炉 脱ガス炉 加熱炉 |
|
|
|
|
一体施工 不 可 |
|
不定形化 |
|
|
|
|
| |
4、おわりに
製鋼プロセスで使用される主なる装置について、そこで使用される耐火物の具備条件と実使用の耐火物について概説した。その中で、ランスなどの付帯設備については割愛した。また、耐火物そのものの設計技術についても同様割愛した。製鉄会社の努力による原単価の低下、輸入品の活用による国際価格との競合からの価格破壊で耐火物業界は未曾有の苦難に直面している。今後、日本の耐火物屋はハード(製造など)は、たとえ外国に譲っても、長年築き上げたソフト(使用法、開発など)を活かして、さらなる新規製品の開発、使用条件に適合する材料選択技術等で今後も世界をリードして行かねばならない。したがって、これから耐火物ユーザーとメーカーの緊密な協調が重要になると思われる。
[ 参考文献一覧 ]
総論 1)吉木文平、"耐火物工学"、技報堂 (1965) 2)杉田清
、"製銑・製鋼用耐火物" 地人書(1995) pp13-24 3) "鉄鋼界"、 5月号、8ー9
(1995) 4)耐火物技術協会資料 5)内田三男、"セラミック"、30、786-787
(1995)
溶銑鍋、混銑車、溶銑予備処理 6)殿村ら、"耐火物"、44[11](1992)639 7)松生昭ら、"耐火物"、37[12](1985)711 8)松生昭ら、"耐火物"、38[11](1986)765 9)半明正之ら、"耐火物"、33[10](1981)564 0)鳴瀬庸一、"鉄と鋼"、 70[6](1984)
474 転炉 11)渡辺昭、"セラミックデーターブック"'89231ー236
12)K.K.Kappmeyer and D.H.Hubble; "High Temperature Oxides
Pa ED.A.M.Alper"(1970)pp.1-76[Academic Press] 13)大日方
ら、製鉄研究(1977)291、p.12158 溶鋼鍋 14)H.Shibata,ILAFA A LAFAR
Congress (1980.11.) 15)森淳一郎 ら、"耐火物"、41、348、(1989) 16)永井敏
ら、"耐火物"、42、418、(1990) 17)浅野貞 ら、"耐火物"、42、518、(1990)
18)八百井秀雄 ら、"耐火物"、45、521、(1993) 真空脱ガス処理
19)城野勝文 ら、"耐火物"、48、22、(1996)
20)桑原達朗、"鉄と鋼"、73(1987)p2157ー216
21)耐火物技術協会、"耐火物とその応用"p371ー373 22)松村龍雄
ら、"耐火物"44[4](1992)238ー224
23)石井章制ら、"耐火物"44[4](1992)245ー25 24)北井恒雄、"耐火物"46[7](1994)
384-38 電気炉、LF鍋 25)セラミックデーダーブック、1988
26)電気製鋼、66、(1989) 連続鋳造 27)安藤満 ら、"耐火物"47[4](1995)194
28)伏見哲朗 、"耐火物"47[4](1995)187 29)浅野 貞、UNITECR '93 (1993) 82
30)宮下芳雄、"耐火物"27[2](1975)55 31)大門雅也 ら、"耐火物"42[11](1990)660
32)西 正明 ら、"耐火物"44[1](1992)36 33)高島 靖
ら、"耐火物"44[12](1992)724-725 34)京田 洋
ら、"耐火物"36[4](1984)218-219 35)安藤満 ら、"耐火物"47[4](1995)195-196
36)荻林成章、"耐火物"46[4](1994)173-174
37)荻林成章、"耐火物"46[4](1994)175
38)中村州児、"材料とプロセス"16(1993)294 補修装置と材料 (吹付) 39)石橋種三
ら、"耐火物"34[9](1982)538-542 40)木谷福一
ら、"耐火物"45[9](1993)540-541 ( 焼付)
41)田中隆志 ら、"耐火物"47[8](1995)413ー414 42)田中隆志 ら、UNITECR '95 3(1995)
42 (溶射) 43)平櫛 ら、"耐火物"33[11](1981)599ー605
44)平櫛 ら、"窯業協会誌"90[3](1982)115-120
45)前田 ら、"耐火物"47[5](1995)382ー389 46)前田 ら、 UNITECR '95 3(1995)
50 |
|
|