 |
鍋の取っ手製作の第2弾。
左は鍋本体と新たに作る取っ手のCAD図面。
今度は卓上フライス盤をはじめ、便利な電動工具をいくつか購入したので、ラクに作れることでしょう。
鍋の取っ手を題材に、プロクソン卓上フライス盤の使い勝手を紹介していきます。 |
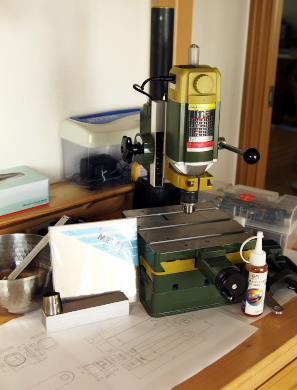 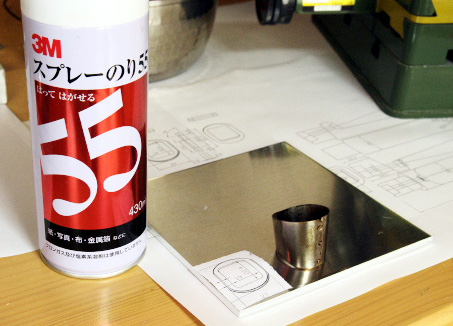 |
写真(左)
卓上フライス盤、エンドミルや工具類、マシン油、など。
机の上で作業します。
写真(右)
アルミ板から、取っ手とジョイントパイプ(右写真に写っている小さな筒状のもの)の間にかませるツバを削りだす。
1/1で印刷した図面を切り取って、スプレーのりで貼り付ける。
スプレーのりは、溶剤系。
木工ボンドなど水溶性ののりを使うと、図面が伸びて寸法が狂うかも知れません。 |
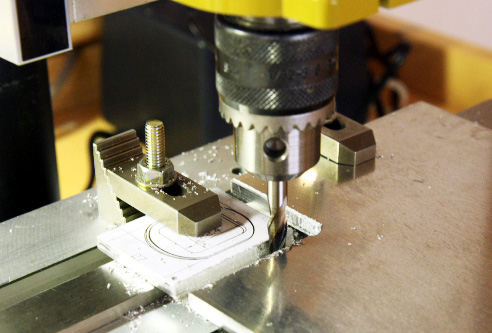 |
部品の外形を削り出しているところ。
奥に見えているのは、フライス盤のオプションで、「高さ自在クランプ」。
アルミ板材料の下に何かスペーサをかませて、フライス盤のX−Yテーブルから少し浮かせてクランプしています。
この状態でテーブルをX−Y方向に動かすことで周囲を切削していく。 |
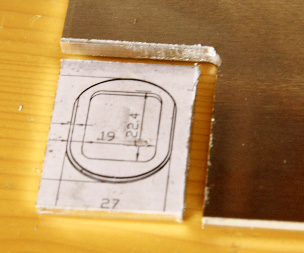 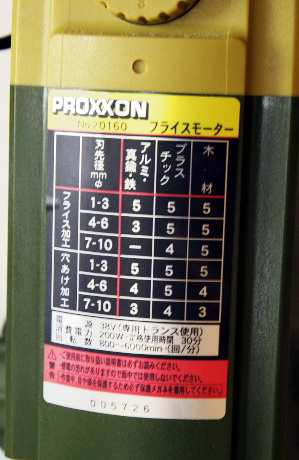 |
アルミ板から切出したところ。
そうそう、調整するのを忘れていましたが、
スムーズに綺麗に加工するには、材料と加工の種類(フライスorドリル)に応じて、回転速度を調整しなければいけません。
フライスモーターに一覧表が貼付けてあるので、これを見て調整しましょう。 |
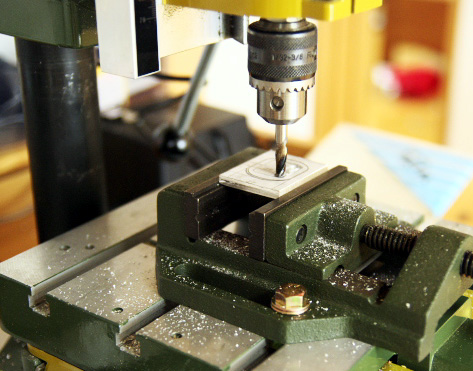 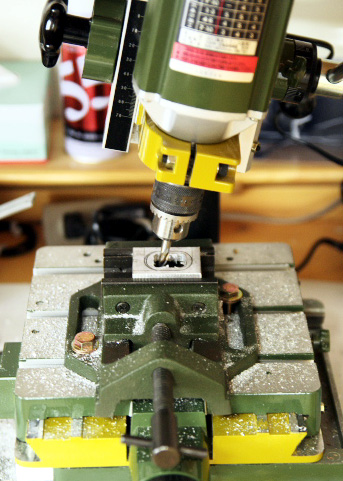 |
写真(左):削り出す部品の周辺を小さく切出したのは、写真の「バイス」(万力)を使うため。これ自体をテーブルにボルト固定する。 簡単に材料を固定できて便利。
写真(右):フライスモーター自体を左右に傾けられるので、斜め加工も出来る。
角度目盛りが付いているけど、あまり信用できない。
加工面を基準にして、刃物の角度を分度器で直接測ったほうが良さそう。 |
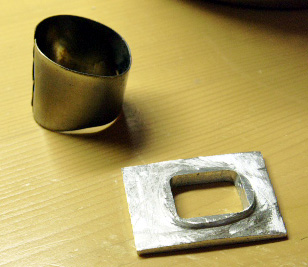 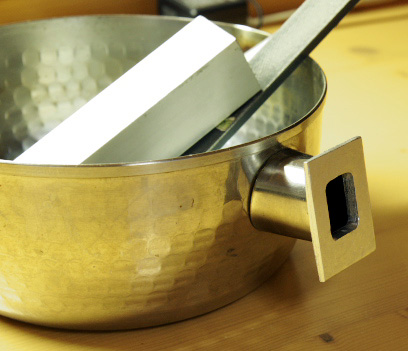 |
写真(左)
フライス盤のあと、ヤスリで微調整(現物合わせ)して取付け部分の形状を削り出したところ。
写真(右)
取付けてみた状態。 |
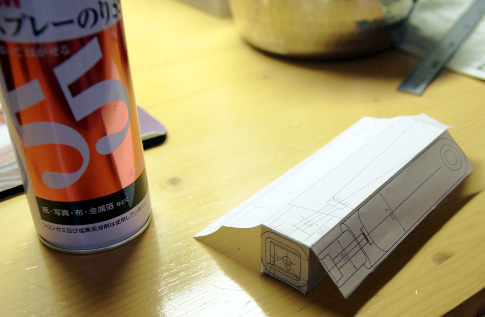 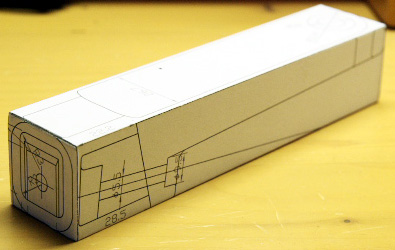 |
取っ手本体の加工に取り掛かる。
図面(1/1)をスプレーボンドで材料(アルミ角棒)に張付ける。 |
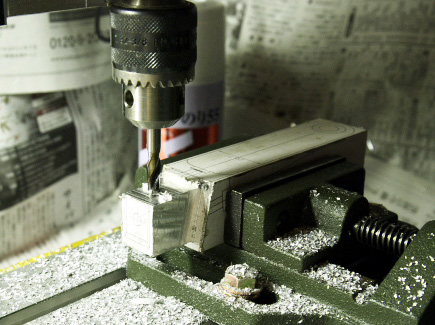 |
鍋への取付け部分。
図面の線に沿って大まかに外形を削る。
削る面を変えるたびにバイスの固定位置を変更。
材料を適切な位置に固定するのに一番時間がかかる。
(材料の固定角度がきっちり出ているか?)
固定さえ出来れば、削るのは一気に進む。 |
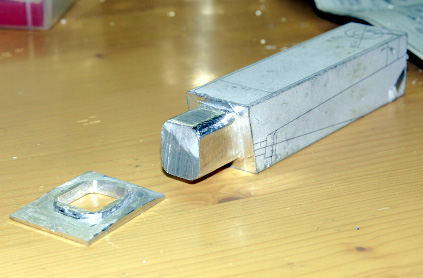 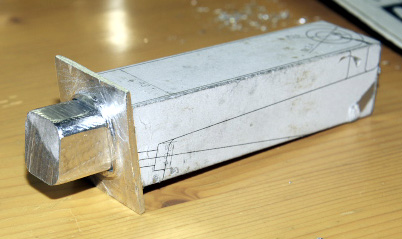 |
部品に合わせながらヤスリで微調整。 |
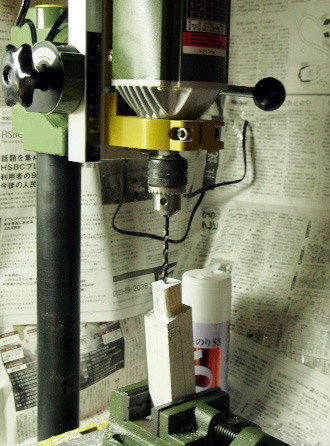 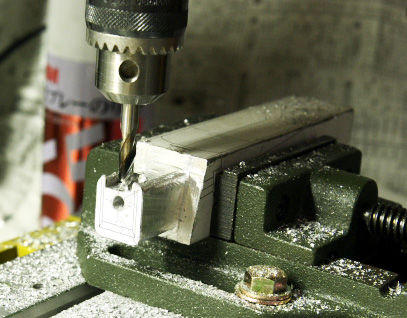 |
写真(左)
固定ねじを通す穴を、ドリル刃で開けているところ。
穴は斜めに開ける。
きっちり角度を出してクランプするのが難しい。
今回は、糸の先に小さな重りを付けて、ドリル刃の向きが図面に描かれた穴の中心をきっちり通るようにした。
写真(右)
鍋側に付いている取付けブラケットが嵌る溝を削り出す。 |
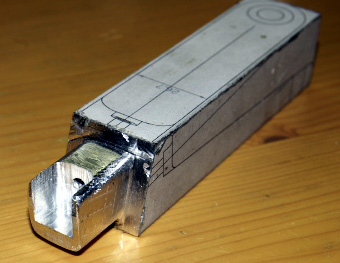 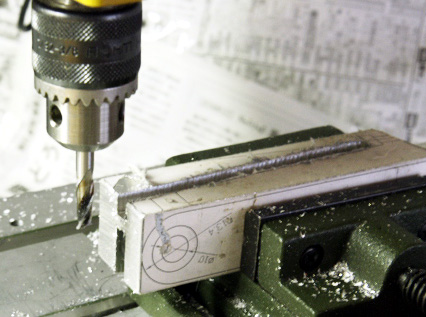 |
写真(左)
削り出した取付け部分。
写真(右)
取っ手の「握り部分」を切り出す。 |
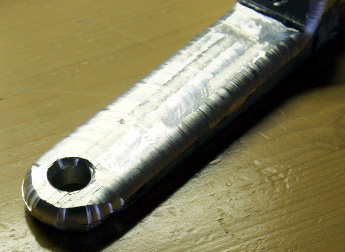 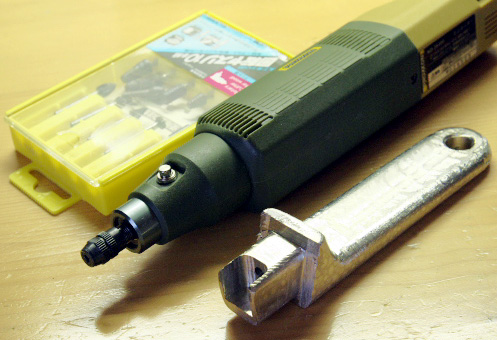 |
フライス盤で外形を削り出した状態。
テーブルはX−Y方向しか動かないので、先端の半円などを削り出すのは厄介。回転テーブルなども売ってるみたいだが高価。
大体削ったら、後は手作業でヤスリ掛け。
縁の丸みは、トリマー用のビットを使用。
本来は木工用だが、アルミくらいなら切込み量を小さくしてやれば削れる。
さらに細かい部分、入りくんだところはルーター等を利用。 |
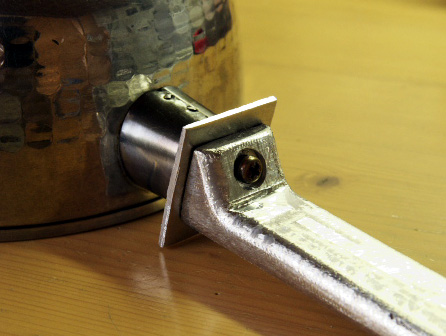 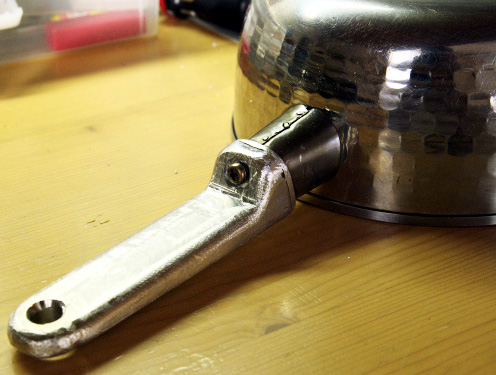 |
写真(左)
表面の荒削りが終わって、取付けてみた。
写真(右)
取付けたまま、根元のはみ出たプレートや取っ手の角部をヤスリで削って丸くした。
これで外形は完了。 |
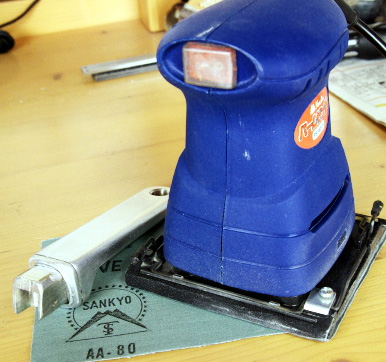 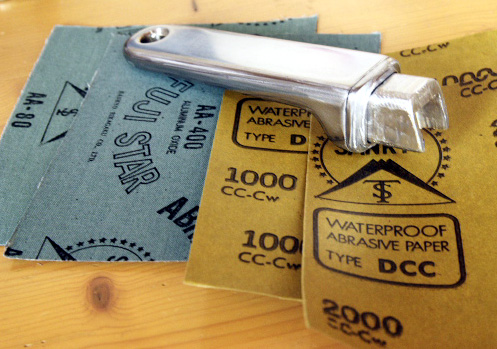 |
パームサンダーを使って、表面仕上げ。
ペーパーは、80番 → 400番 → 1000番 → 2000番の順に使って、表面を徐々に滑らかにしていく。
手でやっていたら大変だけど、さすが電動工具。楽チン。 |
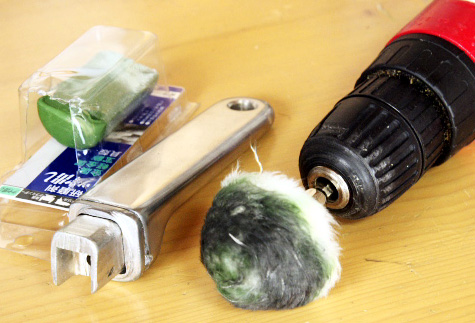 |
最後に、鏡面仕上げ。
回転バフに青棒(研磨剤)を塗りつけ、電動ドリルに取付けて、取っ手表面を磨き込む。
ペーパー掛けが終わった状態では表面は細かい傷だらけでくすんでいるが、青棒で磨くとみるみるピカピカになっていく。 |
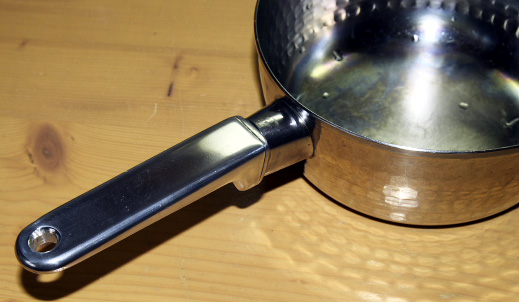 |
完成して鍋に取り付けた。
鍋は一部焦げ付いたりして古びているが、取っ手はピカピカの新品。 |
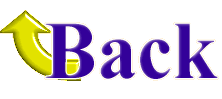 |